SCM "K 230 EVO" Edgebander
Active
SCM Edgebander, Sliding Table Saw, Shaper, Line Drill & More - Prescott, AZ
Prescott, AZ
- Starting Bid : $1,000.00 USD ( ) No Reserve
- 0 Bid(s)
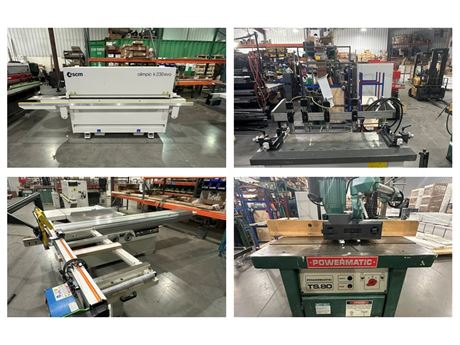
SCM Edgebander, Sliding Table Saw, Shaper, Line Drill & More - Prescott, AZ ( Active #73173103 )
Custom cabinet manufacturer in Prescott, AZ is offering machinery and supplies they no longer need for production.
-
Pick Up Location
6690 Inter-Cal Way Prescott, AZ 86301
-
Make
SCM
-
Model
K 230 EVO
-
Serial Number
AB00011141
-
Year
2019
-
Phase
1 PHASE
-
Voltage
220 VOLT
-
Buyer Inspection Period
By appointment only, contact Thomas Aronson - [email protected] - 941-699-8717
-
Load Out Period
End of auction through August 15, 2025 (by appointment)
-
Estimated Dimensions
125” L x 42” W x 58” H
-
Estimated Weight
1,600 pounds
-
Seller Comment
A non-negotionable loading fee has been established. This includes loading onto a flat bed trailer. Requests for additional labor, crating or pallatization will be extra.
-
Load Fee
100.00
-
Lot Notes
-
page views
39
SCM "K 230 EVO" Edgebander
Automatic single sided edgebander designed to be used for edgebanding straight vertical profiles with coiled material (veneer and PVC) and with strips (high-pressure laminate and solid wood) with a maximum thickness of 3mm.
Edgebanding thickness: .4mm - 3mm (.016-1/8”)
Guillotine capacity: 3.0mm
Feed speed: 30 ft/min.
Panel height: 3/8” min – 1 15/16” max
Minimum panel length: 5 1/2”
Minimum panel width: 2 3/8”
Minimum distance between panels: 22”
Controller. The K 230E is equipped with an Orion 1 Plus controller, fixed, located at the infeed of the machine. It is capable of operating all the work units via soft touch buttons, it pneumatically tilt’s the end trim unit from the control panel, it eliminates the use of micro switches, as well as control the temperature of the glue. It is tilted slightly upward for a more ergonomically friendly position for the operator.
Infeed fence
Edgebanding infeed table
Pressure Beam. All operating units raise and lower simultaneously when the pressure beam is adjusted. No adjustment is required for the glue roller when changing panel thickness. The pressure beam has digital height indicators and a double row of pressure rollers with steel bearings.
Glue Station. Teflon coated glue pot to facilitate glue changeover. Warm up time is approximately eight to ten minutes. Application roller.
Pressure station. One (1) driven roller and two (2) spring-loaded pressure rollers for pressing the banding to the work piece edge.
End Trimming Station. This unit is composed of two independent .25 hp motors mounted on THK guides. End trim utilizes a draw cut system for reduced blade projection on thick panels. The unit comes standard with pneumatic positioning of the unit from the control panel with two preset positions. The unit is also equipped with the “radius” edge feature that rounds over the vertical edge on the corners of a 3mm panel.
Edge Trimming Station. This unit is composed of two independent .5 hp motors operating at 12,000 rpm. The unit is equipped with a combination cutter that allows the operator to manually go from solid wood, to thin material, to a radius, all with the same cutter. All adjustments are carried out with mechanical digital readouts. The unit has top and bottom copy wheels and side copy shoes. The motors have quick release plugs to facilitate tooling changes.
Profile Scraping Unit. Scraping station designed to remove knife marks from thick PVC. The unit is equipped with top and bottom copy wheel and side copy wheels, adjustments are made via mechanical digital readouts. The unit is positioned manually. The unit is also equipped with dust extraction and a collection bin.
Buffing Unit. The buffing unit has two .25 hp motors. It can also be tilted up to 12 degrees to provide a softer, more refined edge finish.
Sound enclosure
Outboard roller support
The listed specifications & information were taken from the manufacturer’s published information, internet research, or seller’s description.
The specifications & information are assumed to be correct; however, in no way, guaranteed. Bidders are encouraged to inspect the machine, call with questions, or contact the manufacturer for more information.
Please log in to view the bid history
LoginNo information available