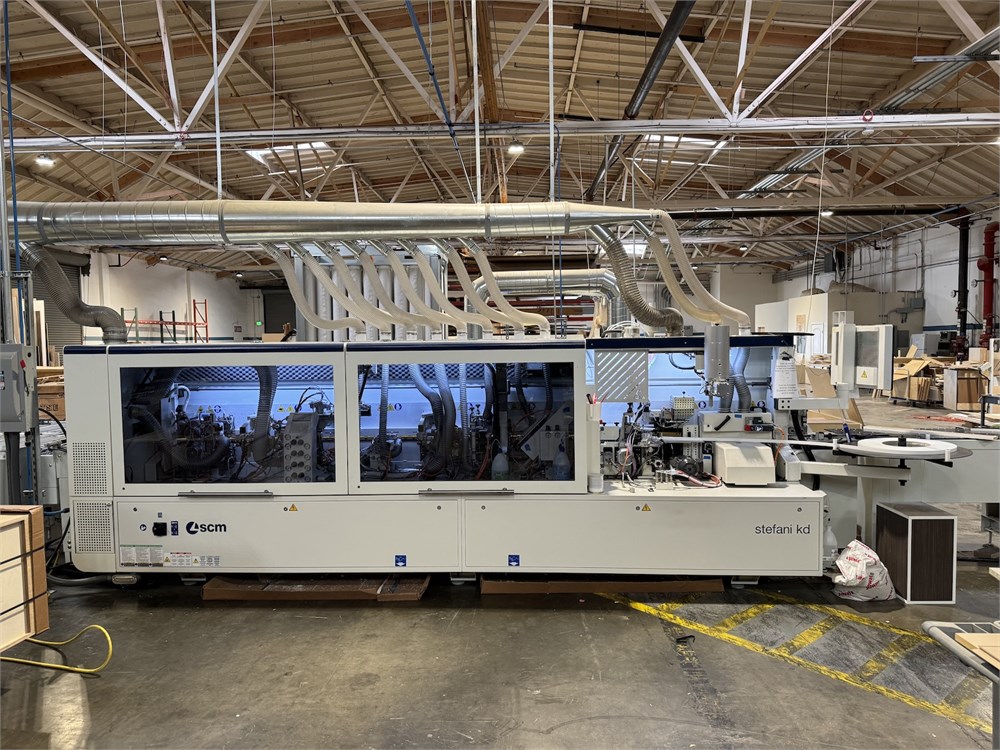
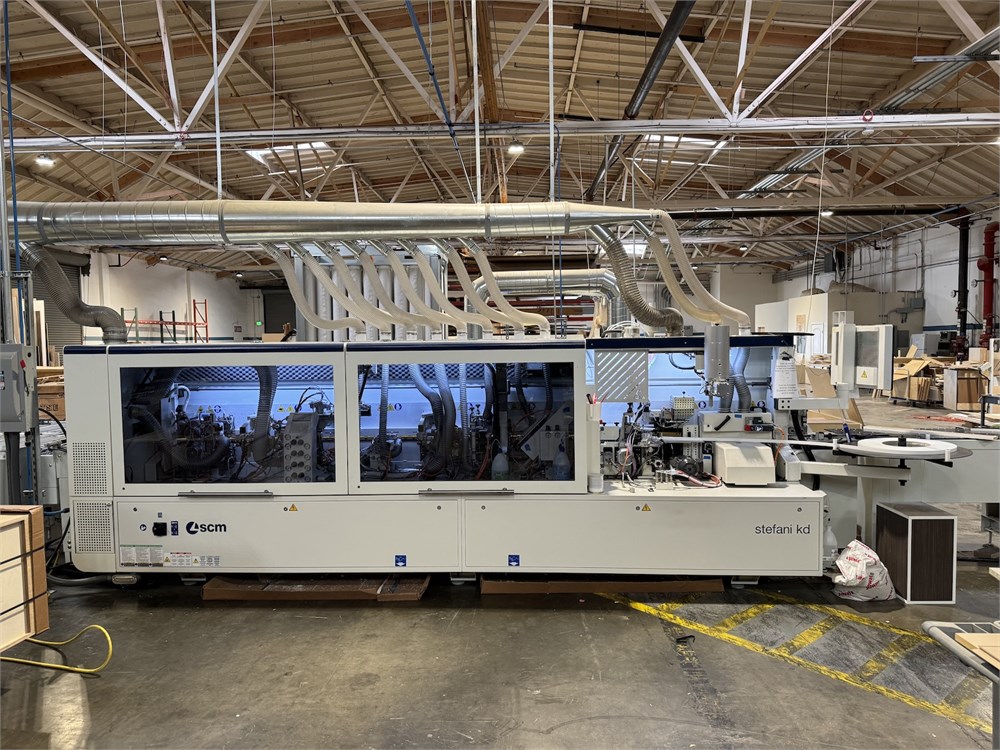

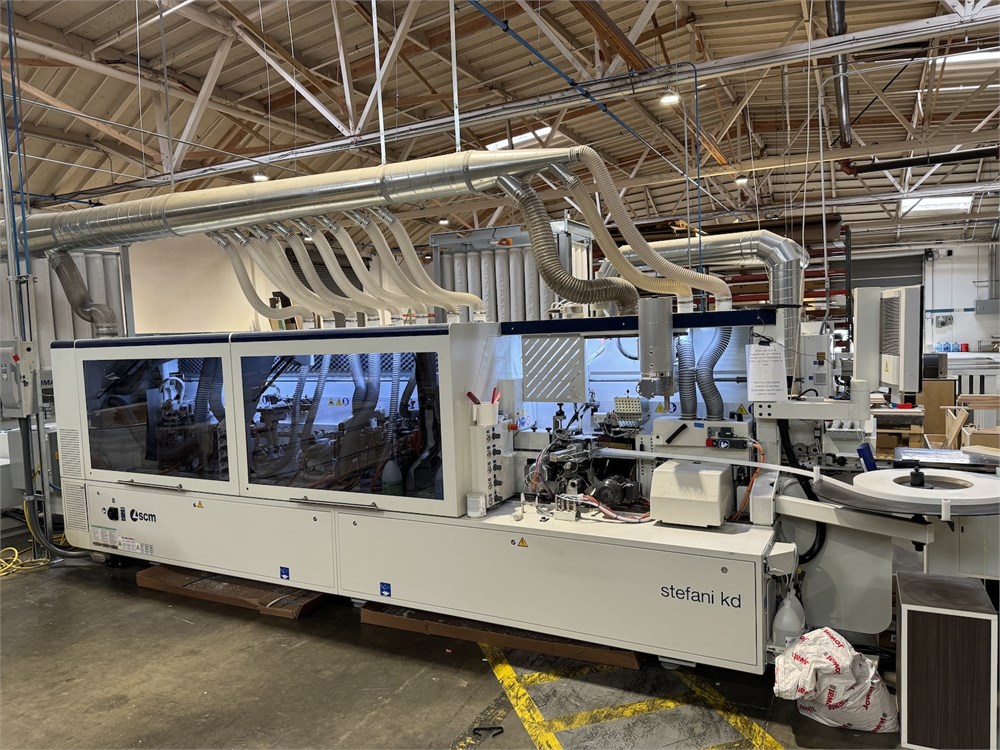
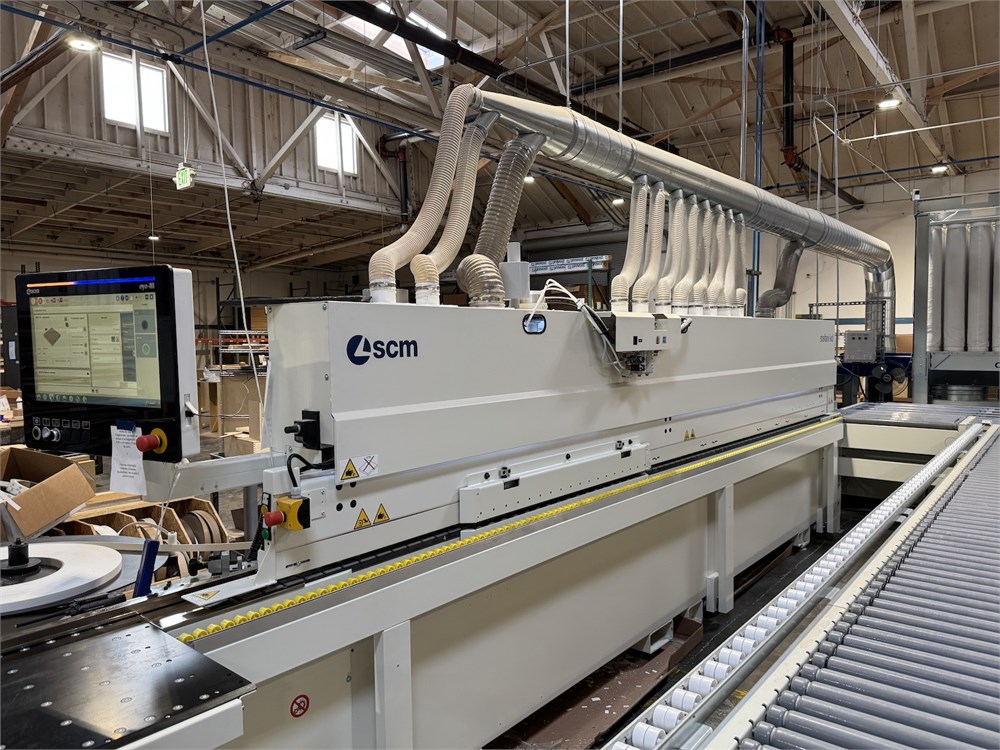
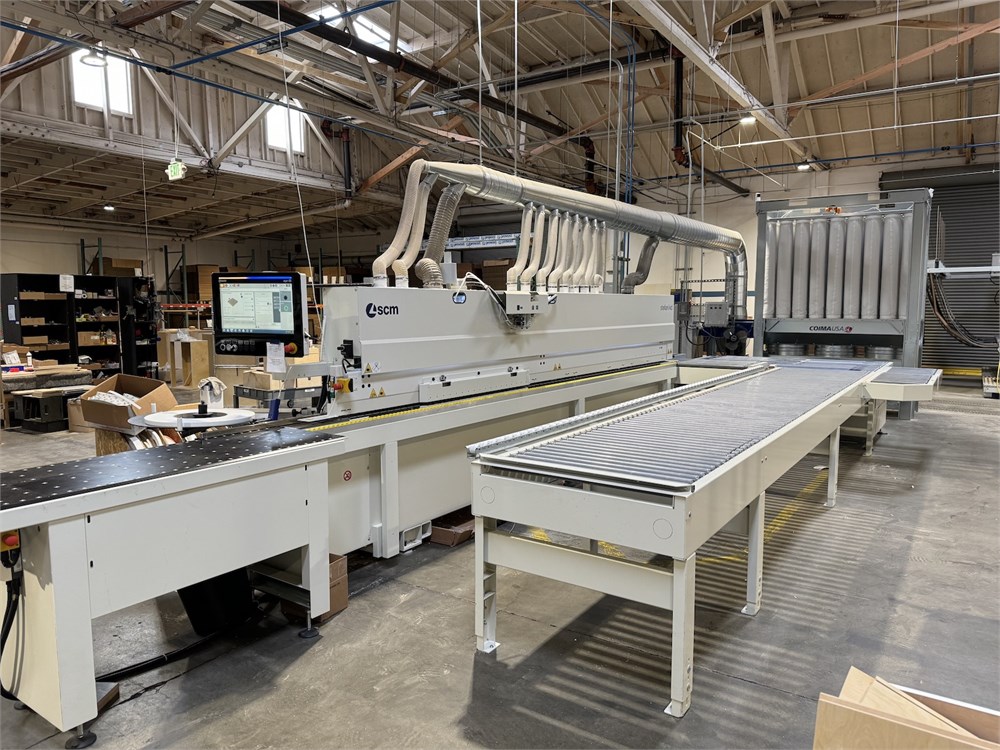
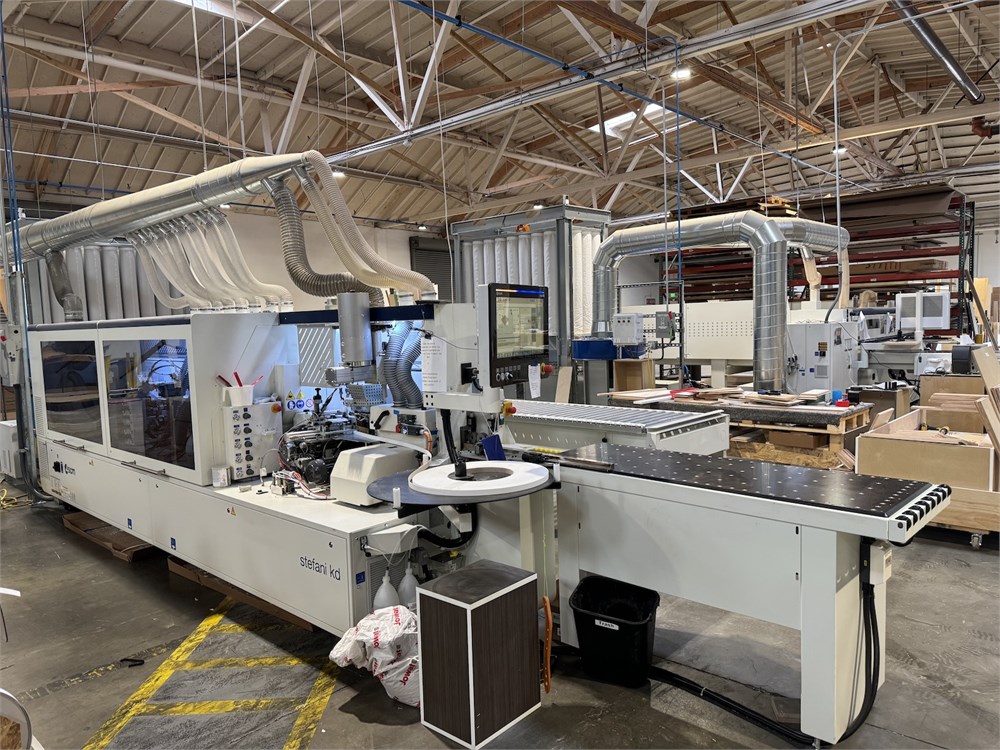
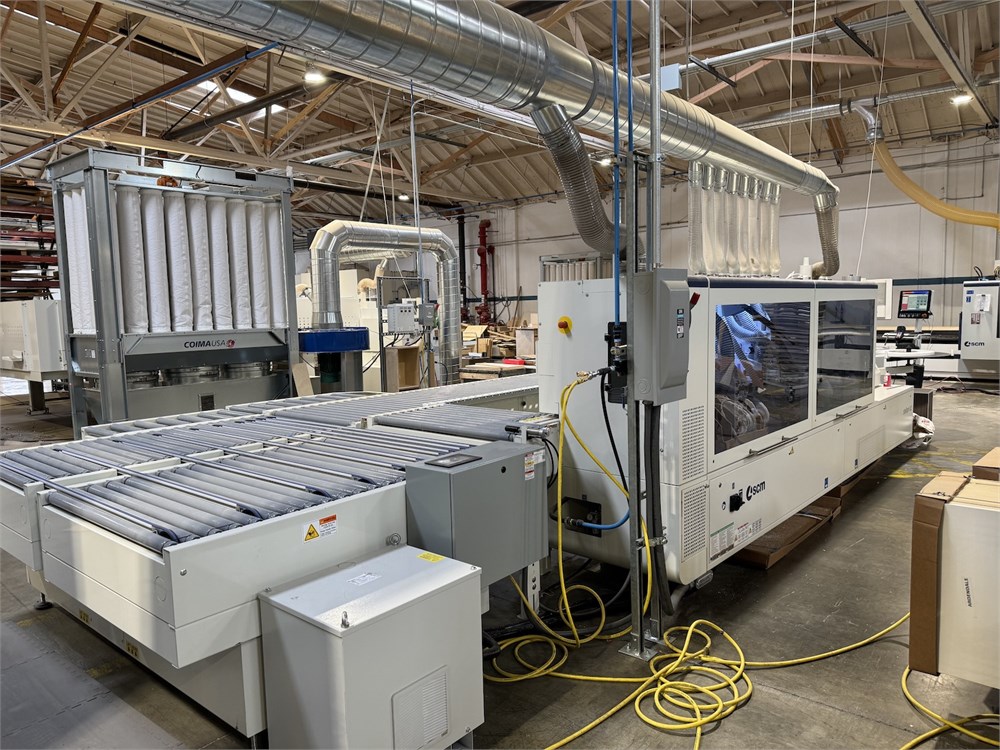
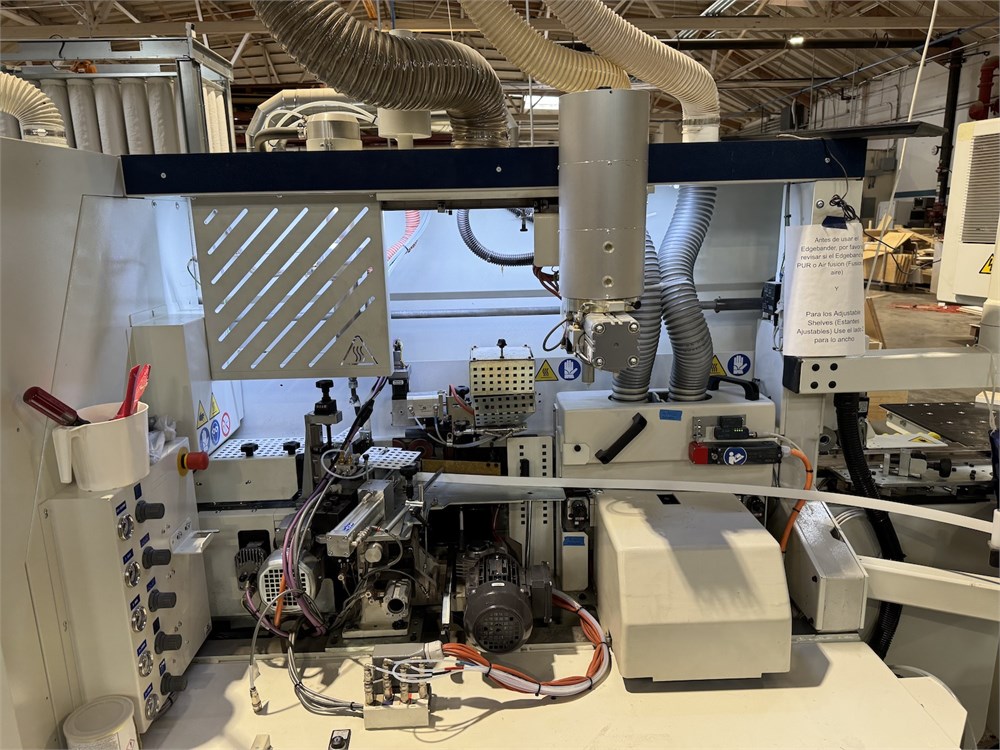
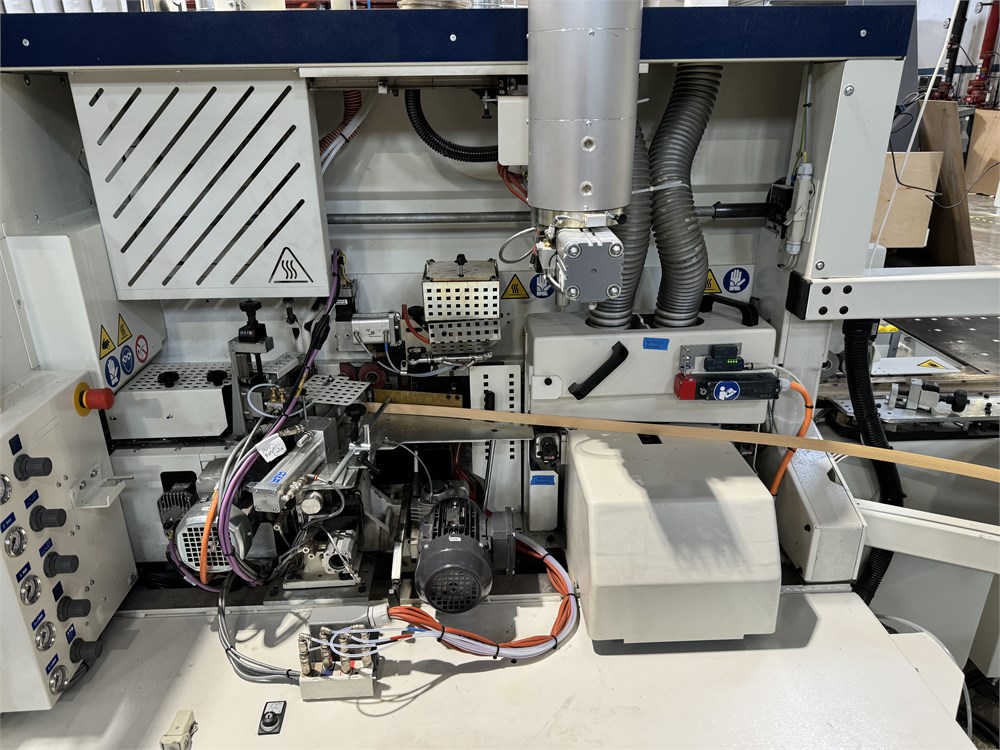
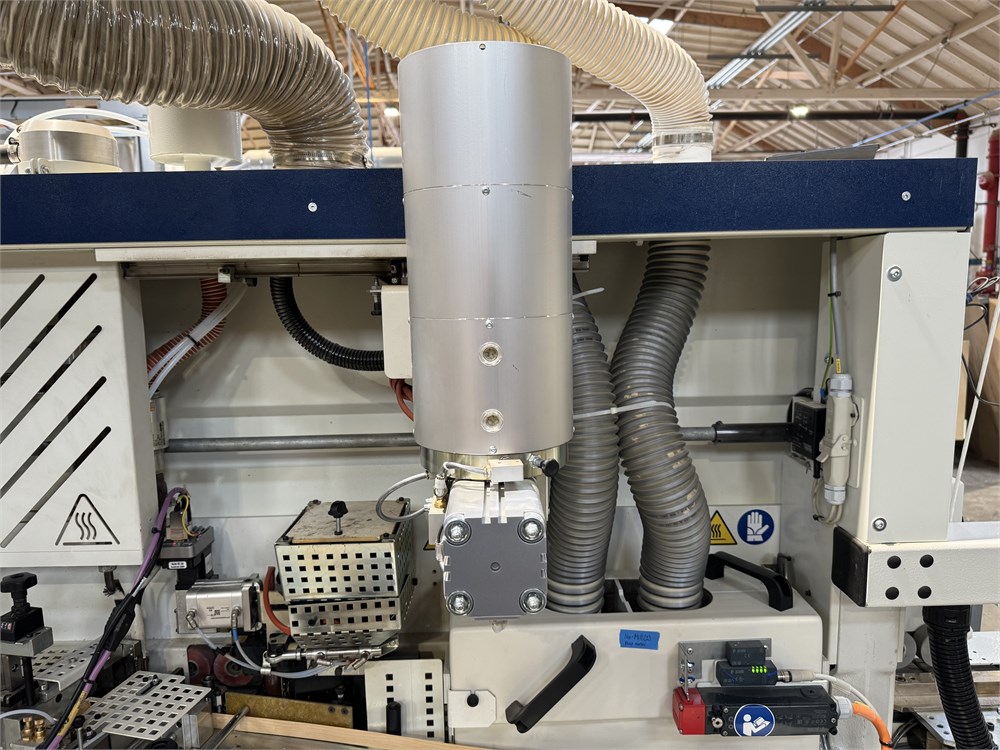
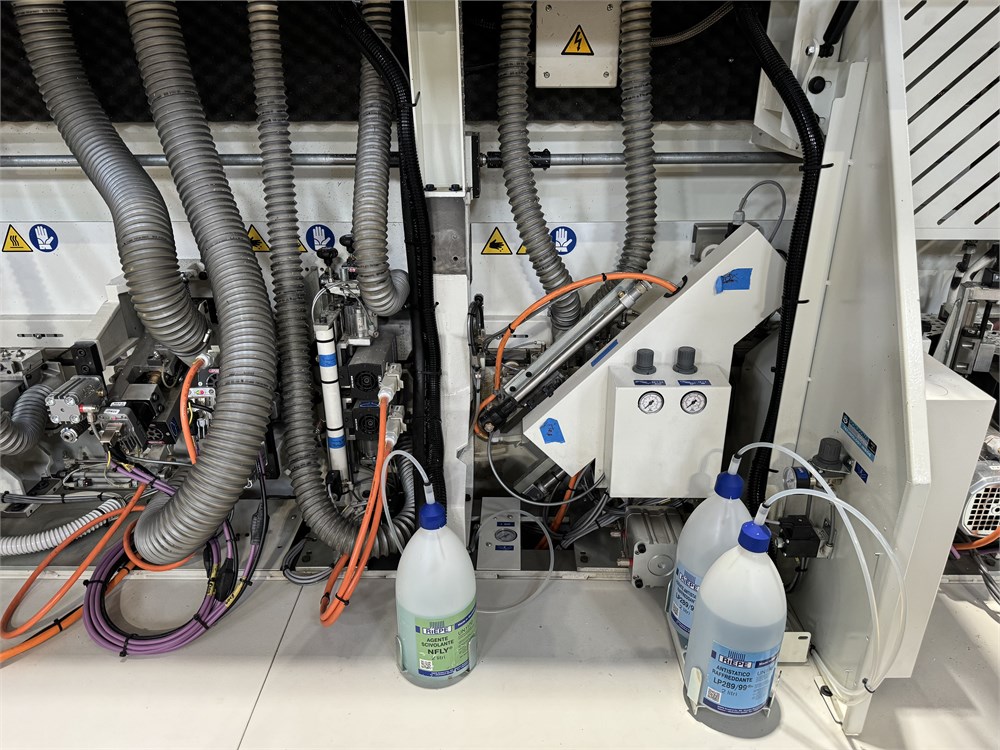
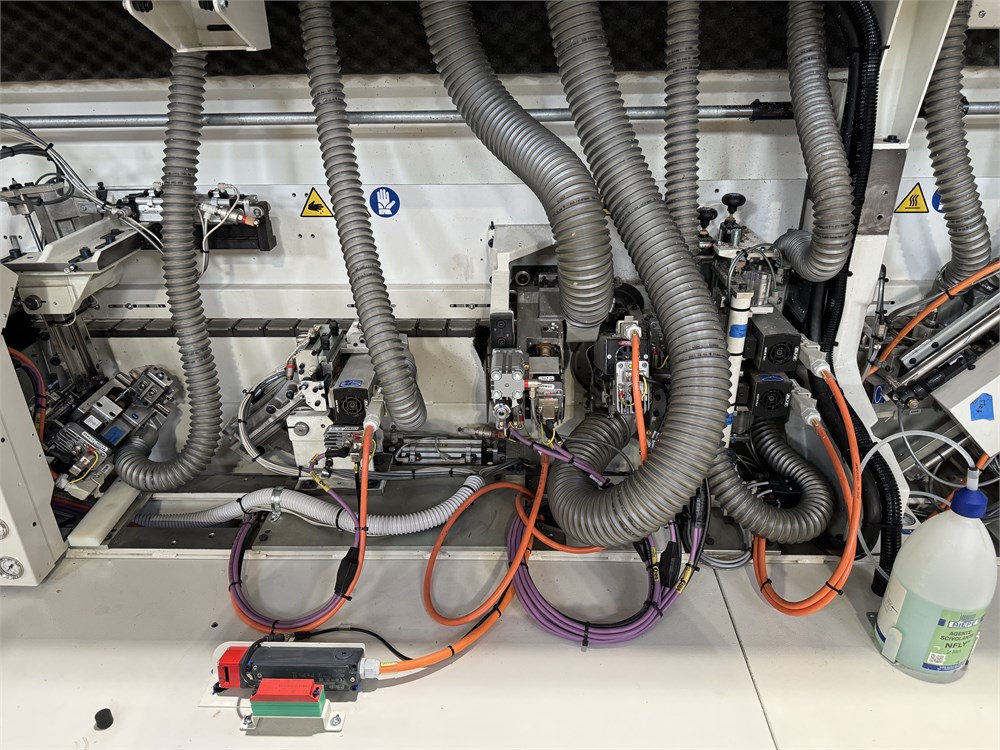
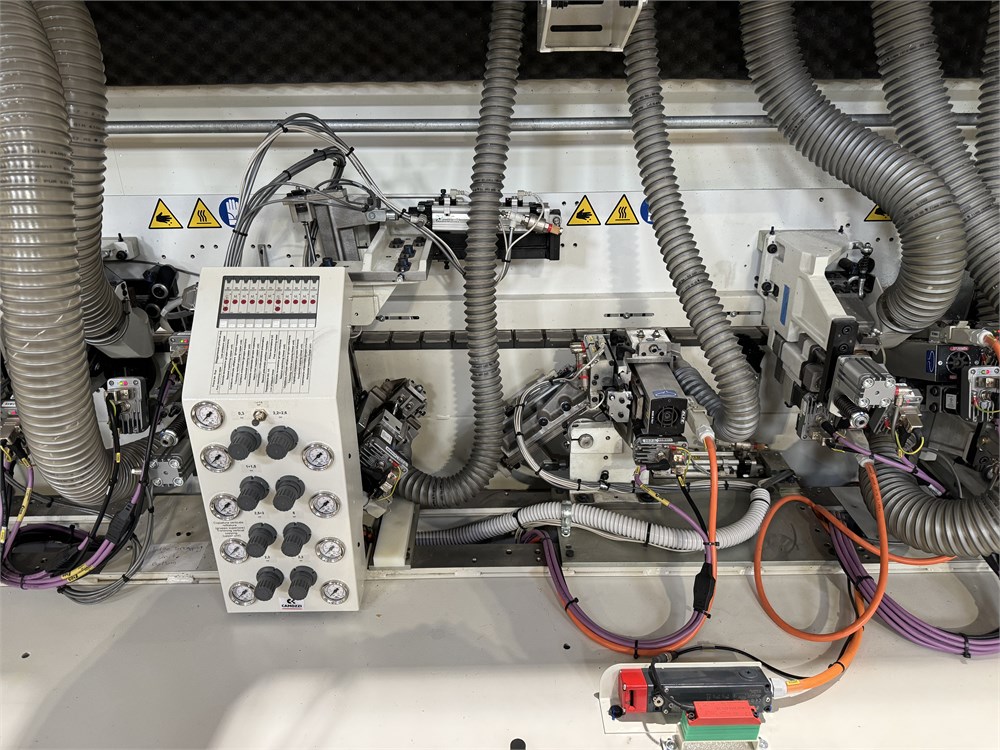
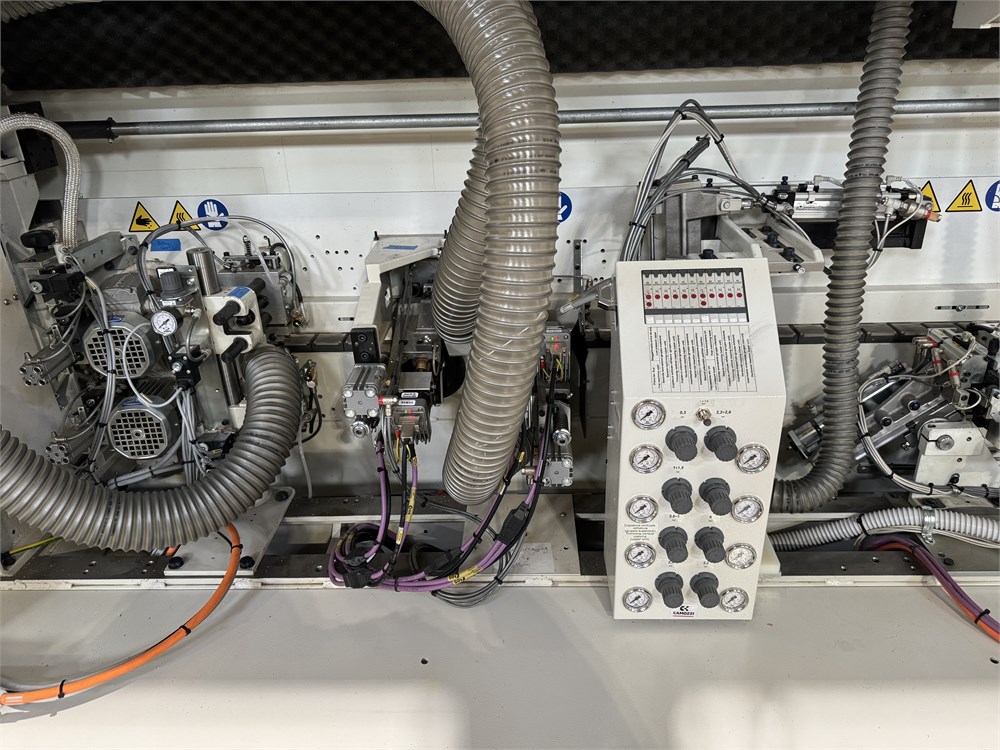
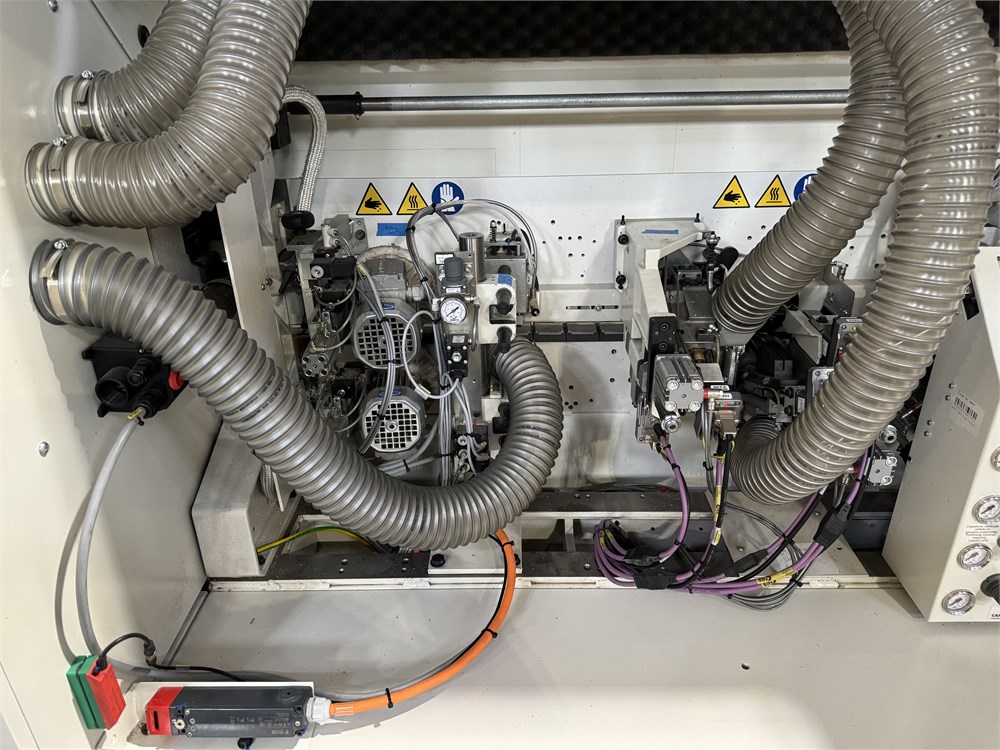
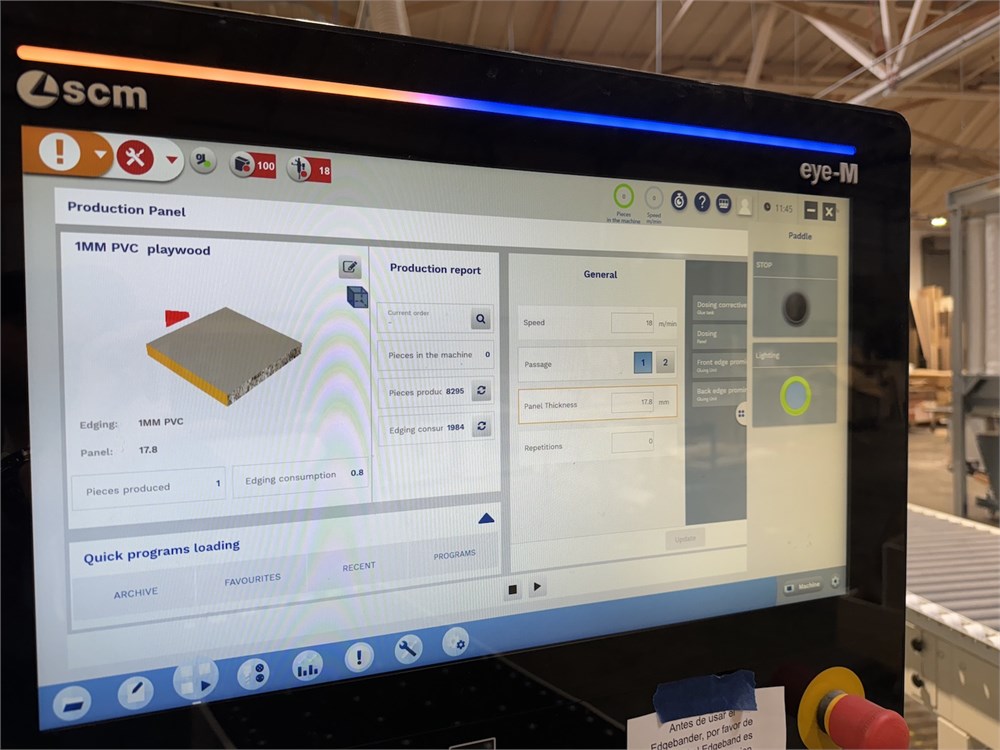
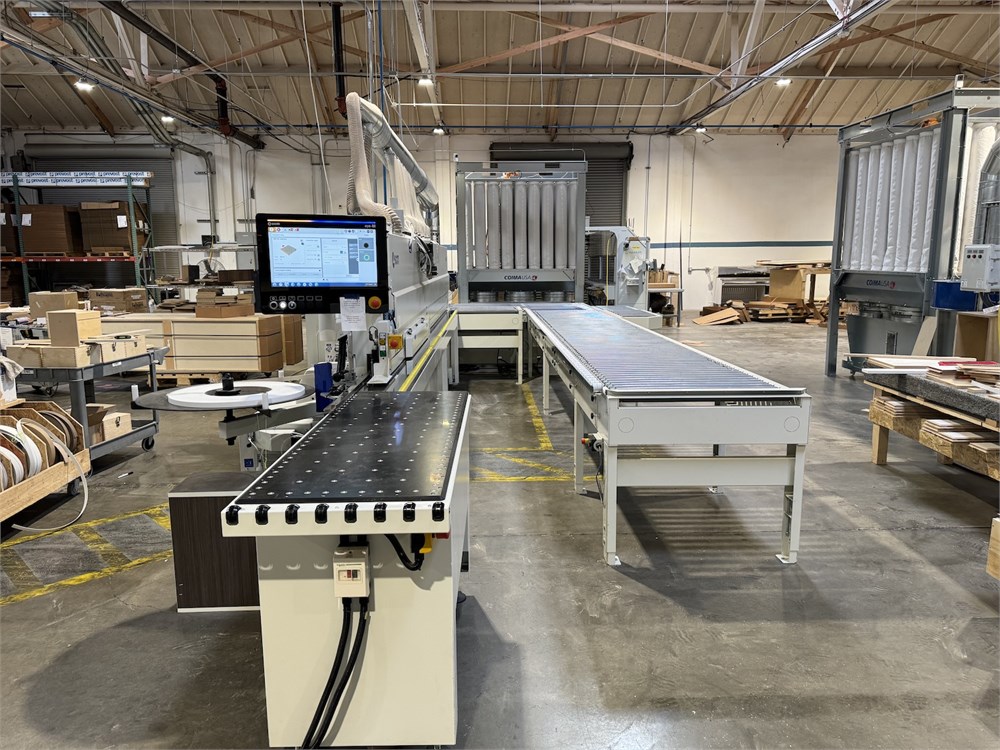
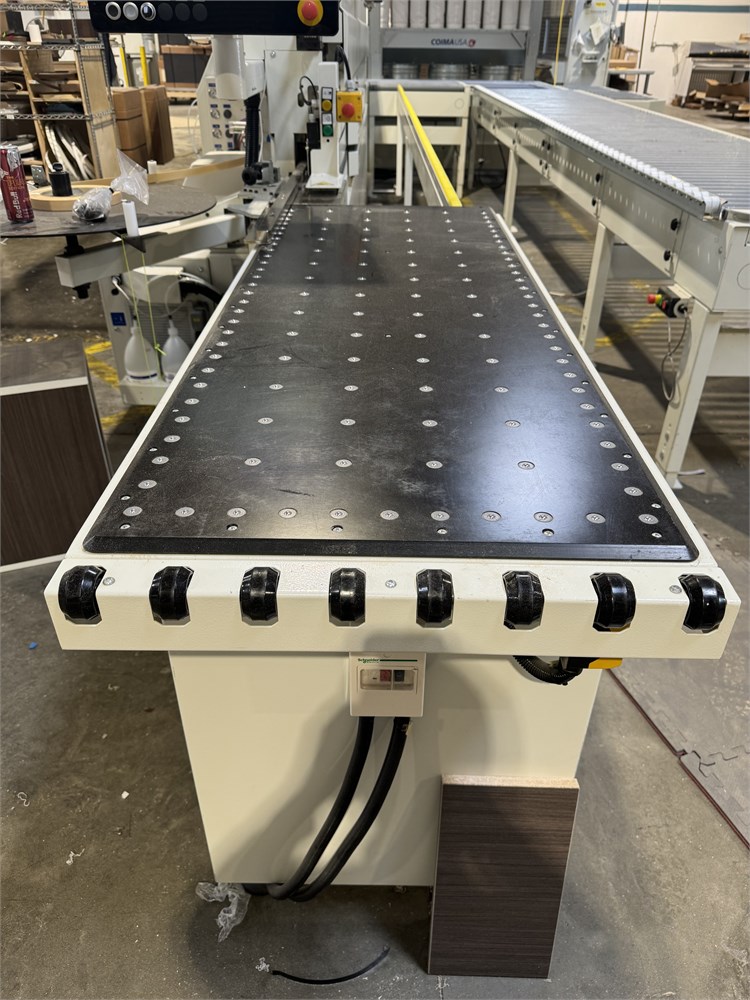
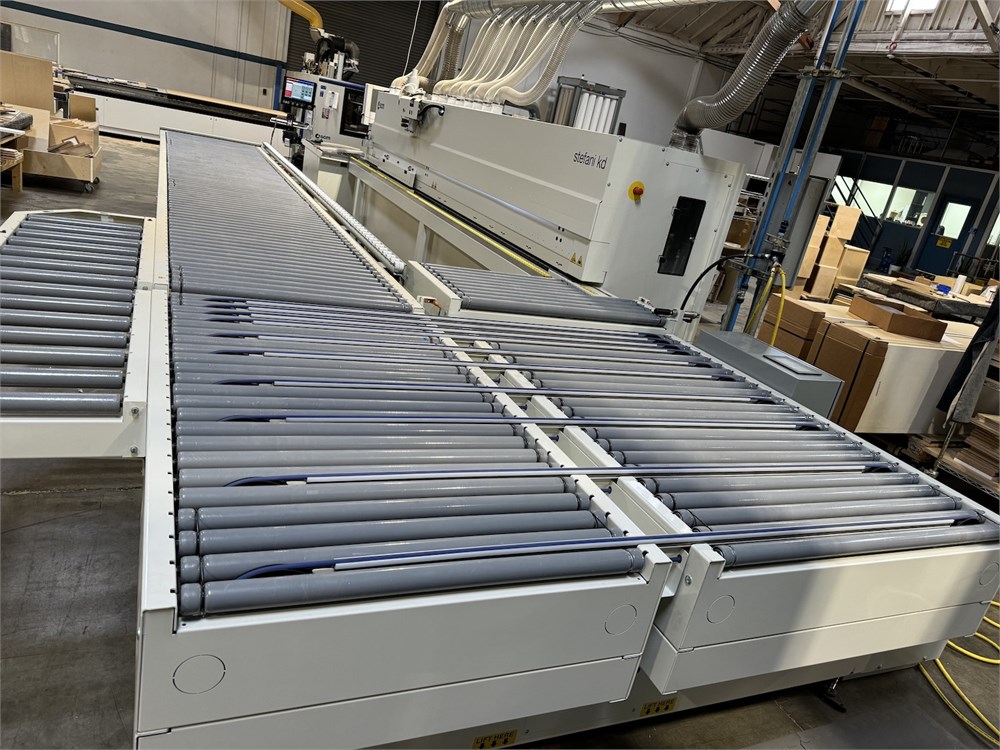
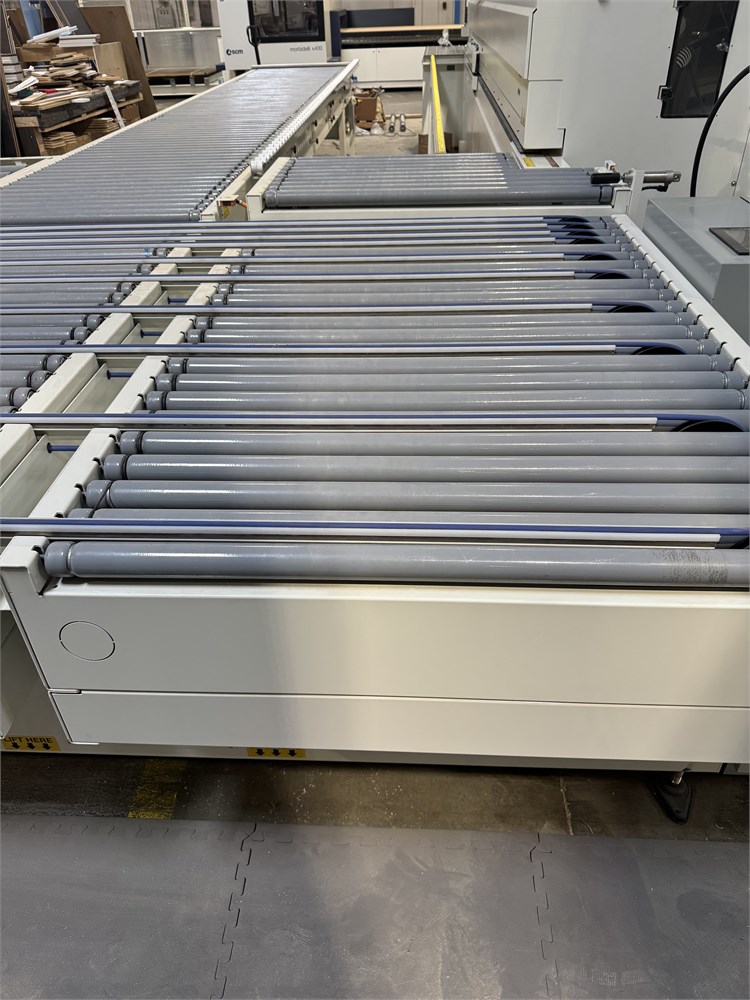
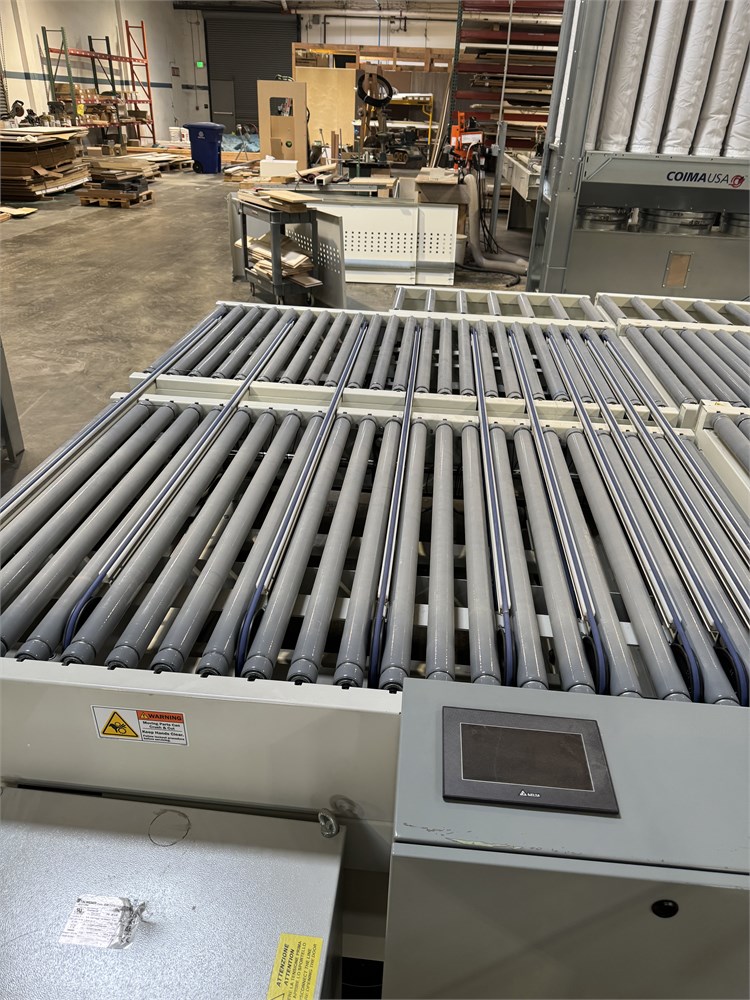
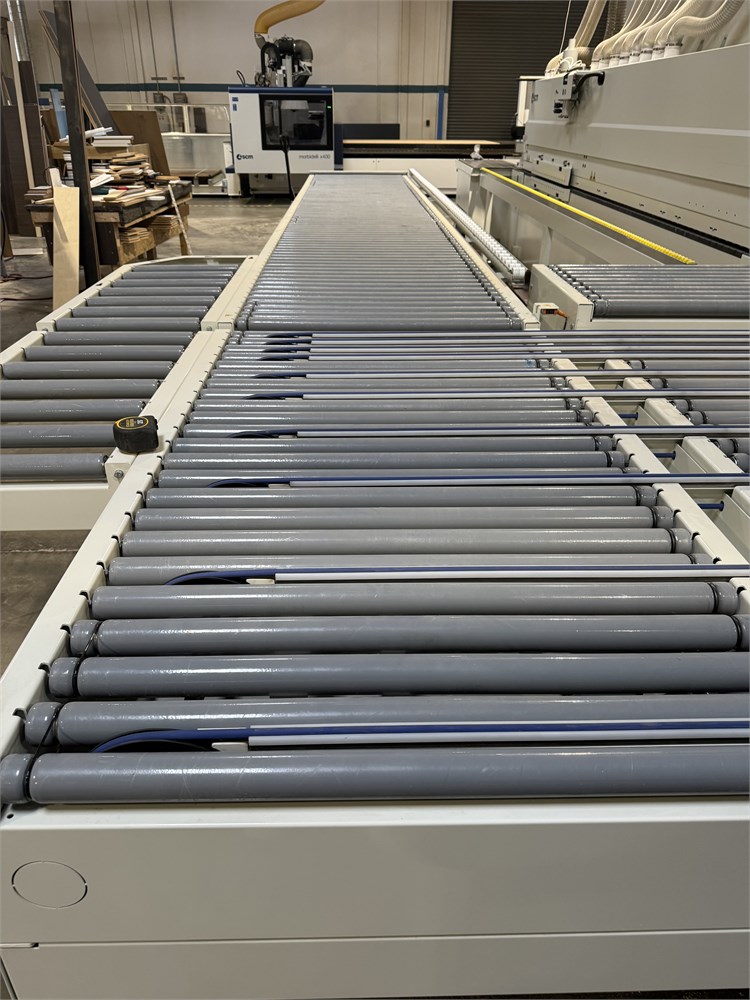
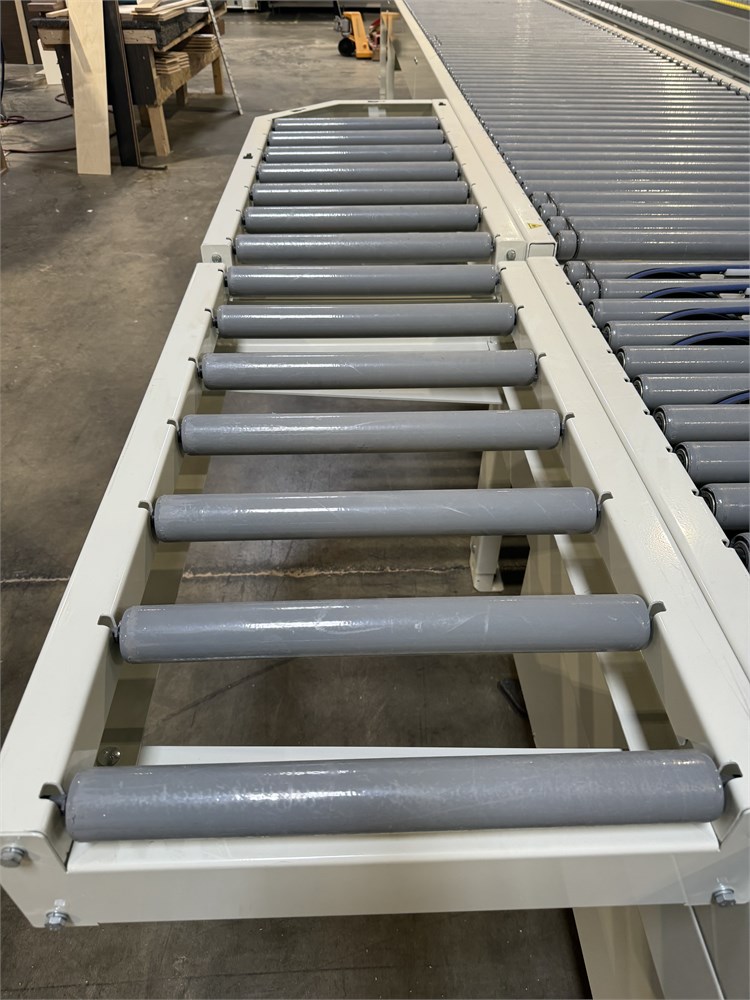
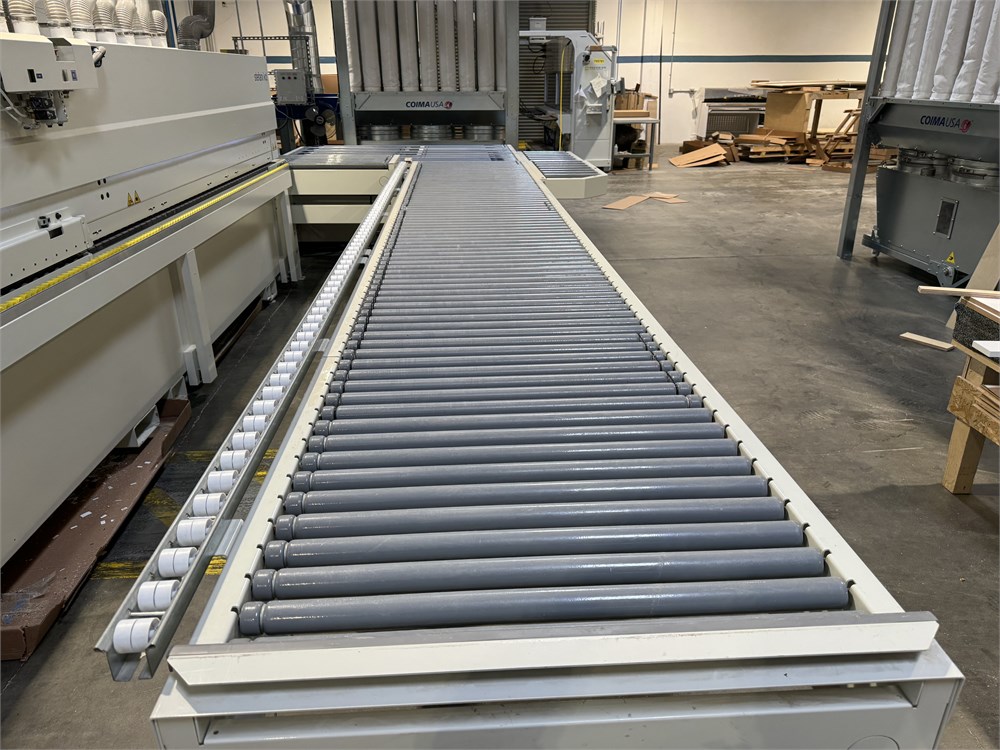
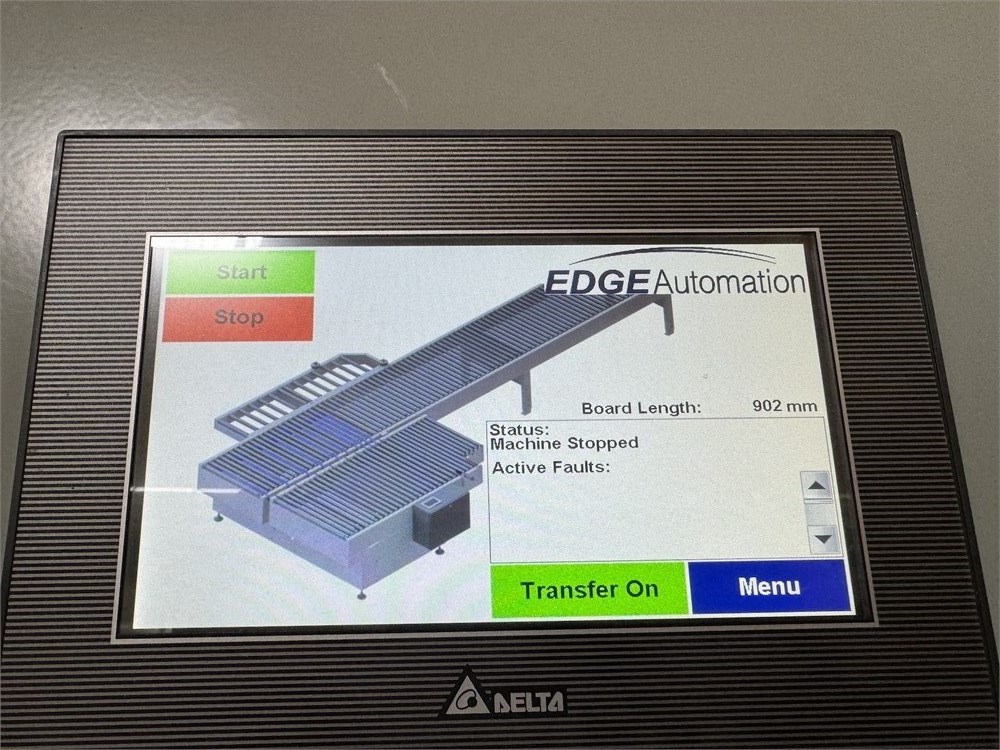
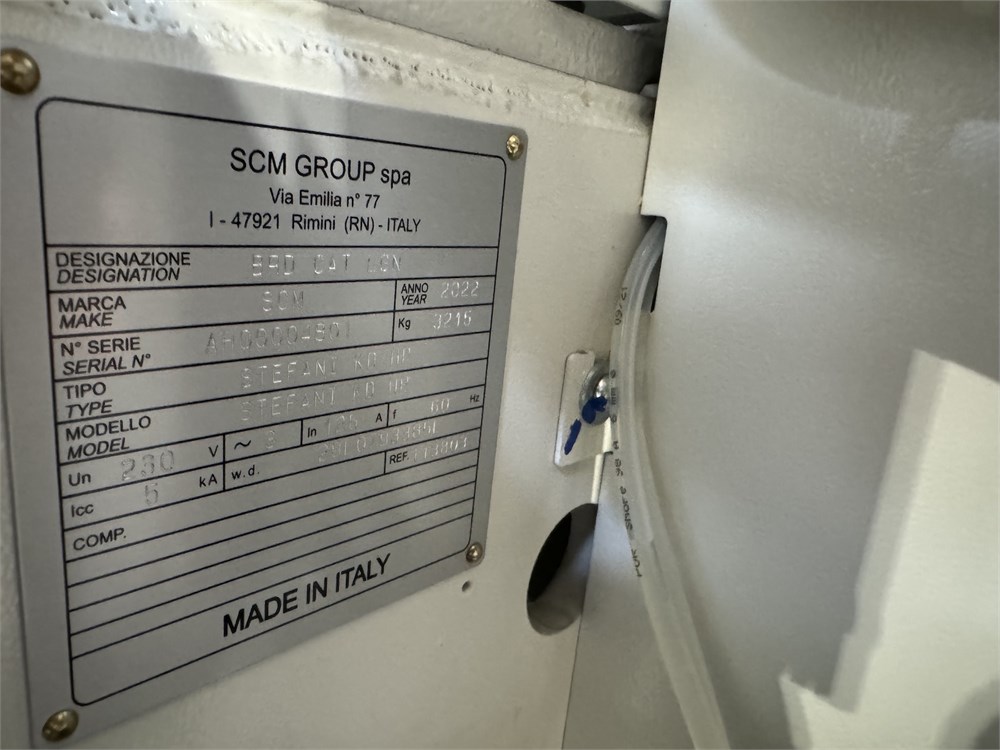
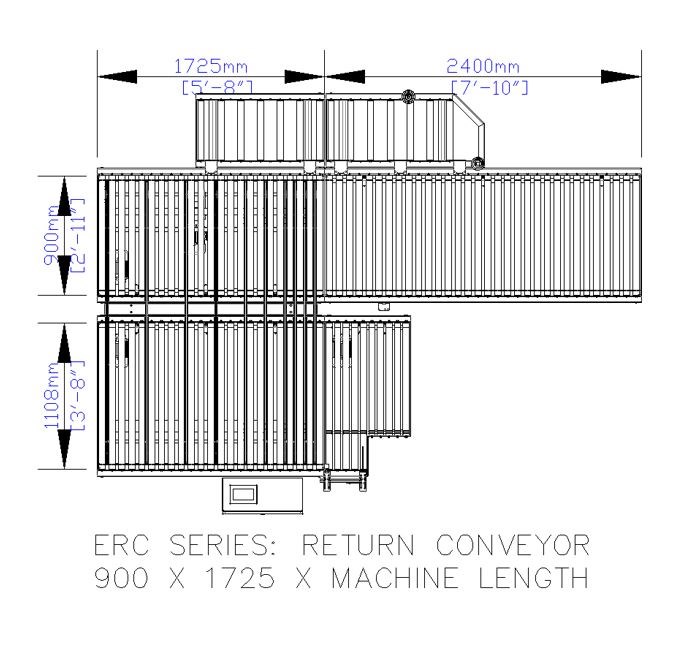
(2022) Stefani "KD HP" Edgebander w/ Air Fusion with ERC Return Conveyor
Ended
Stefani "KD HP" Edgebander with ERC Return Conveyor - Tracy, CA
- 1 Unsold
-
Make
Stefani
-
Model
KDR-HP Air Fusion
-
Serial Number
AH00004801
-
Year
2022
-
Phase
3 PHASE
-
Voltage
230 VOLT
-
Estimated Dimensions
239" L x 65" W x 62" H (edgebander only)
-
Estimated Weight
10,000 Pounds
-
Seller Comment
Seller will disconnect and load onto buyer's flatbed truck/trailer for non-negotiable $3,000 loading fee. Palletizing, crating or other services may be available at an additional cost.
-
Load Fee
3,000
-
Lot Notes
-
page views
24302
SCM "Stefani KD-FRT-Air Fusion" Automatic Single Sided Edgebander (2022) with ERC Edge Automation Automatic Return Conveyor System (2022)
Please see as well attached PDF with full specification quote for this machine.
Automatic single sided edgebander designed to be used for edgebanding straight vertical profiles with coiled material (veneer and PVC) and with strips (high-pressure laminate and solid wood) with a maximum thickness of 12mm. The machine base is a rigid, ribbed steel structure and is designed to provide maximum support for the working units. The ribs provide stability and, at the same time, provide openings in the base to facilitate removal of the chips/dust.
Edgebanding thickness: 0.4mm - 12mm (.016-0.5”)
Guillotine capacity: 3mm
Panel height: 3/8” – 2 3/8”
Minimum panel length: 5 1/2”
Minimum panel width: 2”
Minimum distance between panels: 24"
Feed speed: 33-60 FPM via 2.5 HP motor with gear box
Air Floatation Table on Machine's Infeed, 23.6" x 62.9"
PC 21” Controller EYE-M Controller
Maestro Pro Edge controller, a 21” industrial multi touch screen. Comes standard with a Windows operating
system. Capable of storing an unlimited number of programs. Monitors statistical data, as well perform diagnostic functions and program functions. 1920 x1080 resolution, intuitive interface. Monitors the number of panels processed, the amount of material applied, the number of hours run, the distance the feed track has turned, etc. Maintenance schedules are monitored for various stations throughout the machine. Swivels 270 degrees for easy access.
Electronic Positioning Of The Top Pressure Beam
All operating units raise and lower simultaneously when the pressure beam is adjusted. No adjustment is required for the glue roller when changing panel thickness. The pressure beam has two rows of staggered pressure rollers with steel bearings. The height of the pressure beam is electronically programmable through the controller.
Infeed Fence
The infeed fence has a mechanical digital indicator to position the fence and determine the stock removal. It is also equipped with a
pneumatic panel spacing device to prevent the operator from feeding the panels to close to one another.
“RT-E” Pre-Milling Station
To rectify/clean panels already sized and squared before the edge is applied. The unit is composed of two (2) 3 HP/12,000 RPM high frequency motors with jumping action controlled through the PLC. The cutting heads are adjustable vertically. The unit is equipped with copying devices which guarantee that material removal is consistent on long or slightly out-of- square panels. 64mm tall diamond premill cutters with replaceable
inserts come standard.
Anti-Adhesive Unit
The machine comes equipped with an anti-adhesive unit positioned prior to the pre milling unit. It prevents the buildup of glue on the top and bottom of the panel. The unit comes with two independent nozzles and a tank of anti-adhesive liquid.
“QMS” Glue Station
Automatically supplies the glue pot with the proper amount of glue on demand. The level of the glue in the glue pot is monitored by a sensor insuring the proper level. The pot is smaller, the glue is turned over faster as a result. The hopper holds in excess of 10 lbs.
of glue and has sight glass to see what the level is. Teflon coated glue pot to facilitate glue changeover. Warm up time is approximately eight to ten minutes.
SGP Glue Pot with CNC Control of the Glue
Quick heat up time due to the small glue pot. Reverse rotation of the glue roller for the application of solid wood. Double Thermo Regulation for easy use of both EVA and PUR glue. Color change and glue pot cleaning are able to be completed in minutes, as opposed to hours. CNC control of the amount of glue being applied, specific to the program, is standard. Through the controller the operator can change the amount of glue being applied depending on the substrate of the panel. The purging process is CNC controlled as well when changing glue colors or going from EVA to PUR glue.
Servo Driven Pressure Section
There are a total of four (4) pressure rollers for pressing the banding to the workpiece edge. The first roller is powered and applies pressure pneumatically. It is also Teflon coated to prevent the banding material from slipping. The three idle rollers have opposing one- degree tilt to provide extra pressure along the top and bottom edge. The unit comes standard with a servo driven motor for positioning. This eliminates the need for the operator to manually adjust the unit and helps reduce changeover time. The pressure section is also equipped with pneumatic jumping so the unit activates exactly on the leading/trailing edges. Standard is the edge detecting sensor that will shut down the feedtrack when there is no material present to be applied. Equipped with I-Glue, locks the glue roller in place at the end of the panel eliminating any excess glue.
Air Fusion+ E Device for Edge Application (15 MT/MIN)
Application of the co-extruded and pre-glued edge by means of high temperature.
“K-SEL 2” End Trimming Station
This unit is composed of two (2) independent 0.5 HP/12,000 RPM motors mounted on THK guides. End trim utilizes a draw cut system for reduced blade projection on thick panels. The unit comes standard with automatic tilting of the unit from the control panel with two preset positions. When operating in conjunction with the corner rounding station the unit is equipped with two position pneumatics to leave the material long, thus allowing the corner rounding unit to have a seamless finish.
Flush Trimming Station
Two (2) independent 1.0 HP/12,000 RPM motors. The unit comes standard with two position pneumatics and is capable of cutting flush or leaving an overhang. Equipped with vertical copy shoes with digital indicators. Motors have quick release plugs to facilitate tooling changes. Pneumatic in/out positioning is standard.
"R-HP" Multi-Edge 2R Trimming Station Servo Driven
The top and bottom trim station has two independent 1.0 hp motors operating at 12,000 rpm. Large diameter vertical and horizontal copying devices with precise digital indicators. The unit is equipped with a servo driven motor to go from one material thickness to another through the controller. Top trim unit three roller nesting kit comes standard, beneficial when running panels with grooves and/or 35mm hinge holes.
“ROUND-K” Corner Rounding Unit
Two (2) independent 0.8 HP/12,000 RPM motors that slide on THK guides ensuring the highest quality finish. Unit is designed to work as an additional set of trimmers for rounding the top/bottom as well as the front/rear corners of work piece with 3mm PVC edges. The unit is equipped with front and lateral copying devices and pneumatic blowers to clean the panel. Dust shrouds surround the cutter and travel with the unit as it trims. The unit can go from thin tape to 3mm PVC, through the controller, with no manual adjustments by the operator.
“RAS/1000” Profile Scraping Station
The profile scraping station designed to remove knife marks from thick PVC. The unit is equipped with pneumatic in/out positioning through the controller. It has a large diameter horizontal copy wheel and side copy wheel device with digital indicators. It
features a quick knife replacement system and comes with 3mm knives. The unit is also equipped with dust extraction. Top scrape unit three roller nesting kit comes standard, beneficial when running panels with grooves and/or 35mm hinge holes.
“RCA/2C” Glue Scraping Station
The glue scraping unit is for the finishing of thin PVC. It is equipped with two throwaway knives, vertical rotating copiers and blowers for tool cleaning. The unit is equipped with on/off pneumatic exclusion.
“SPN” Buffing Unit And Hot Air Blower
The buffing unit has two (2) 0.25 HP/3,000 RPM motors. The unit cleans and polishes the panel edge. The unit oscillates to utilize the full width of the wheel and prevent rounding of the panel’s leading edge. The hot air blower is designed to brighten the edges of thick PVC that can sometimes discolor during the machining process. The unit consists of a single hot air blower with adjustable heat range and a directional heat shield for coverage from the top to the bottom edge.
Dust Extraction
Working units are individually ported on the top of the safety enclosure for maximum efficiency, per the drawing.
Lighted Sound Enclosure
Outboard roller support
EA ERC Return Conveyor
See attached drawing of conveyor layout
12" - 98" panel length
2.25" - 64" panel width
3/8" - 2-3/8" panel thickness
66 pound maximum panel weight (less than 27.5" panel length)
100 pound maximum panel weight (over 27.5" panel length)
24" panel spacing at 40 FPM
28" panel spacing at 60 FPM
7" touch screen controller
Panel rotating device
Panel kicker device
35.4" x 62.9" receiving conveyor
84" L x 22" W outboard conveyor
304" L x 40" W return conveyor
3 phase/480 V
Dust pipe and flex hose NOT included
Marketplace items are sold ‘as-is’ and ‘where-is’ without refunds or guarantees. Payment is due 48 hours after offer acceptance; buyer arranges freight within 7 days after offer acceptance.
The listed specifications & information were taken from the manufacturer’s published information, internet research, or seller’s description.
The specifications & information are assumed to be correct; however, in no way, guaranteed. Bidders are encouraged to inspect the machine, call with questions, or contact the manufacturer for more information.
Please log in to view purchase history
LoginPlease log in to post a question
Login
There are no questions for this listing.