2015 Viet "Opera 5-4.3 SLLF" Calibrating Sanding Machine
Ended
By order of secured creditors! Assets moved Lebanon New Jersey
- Winning Bid : $76,250.00 USD Sold
- 105 Bid(s)
- High Bidder: J****n
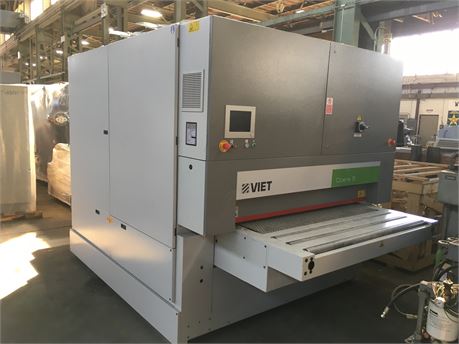
2015 Viet "Opera 5-4.3 SLLF" Calibrating Sanding Machine ( Closed #8642826 )
By order of secured creditors, this Very nice late model Viet will be sold to the highest bidder. Asset has been relocated to rigger location in Lebanon New Jersey. Rigger will load machine for a flat rate of $1,000.00
-
Pick Up Location
Lebanon New Jersey
-
Make
Viet
-
Model
Opera 5-4.3 SLLF
-
Serial Number
5912239
-
Year
2015
-
Phase
3 PHASE
-
Voltage
460 VOLT
-
Load Out Period
October 16, 2017
-
Estimated Dimensions
-
Estimated Weight
-
Seller Comment
This unit has a non negotiable load fee of $1,000.00
-
page views
4412
OPERA 5-4.3 SLLF
BASE - 2620 FOR MACHINE WITH 4 UNITS
GENERAL DESCRIPTION
Prepared for fitting: 4 units
Main Characteristics
Machine
· Frame of carbon steel made up of electrowelded profiles
· Adjustable 55SH rubber coated and grooved pressure rollers
· Designed and manufactured in accordance with "CE-Norms".
· Belt change on left side
· Hexagonal wrenches kit for routine maintenance
Electric cabinet
· "Check panel" alarms with LED
· Automatic Star/Delta starter for main motors
· Padlockable main switch
· Termic relais protections on all motors
· Ampermeter for all main motors
· Electronic digital readout with automatic thickness positioning
· Motor protection IP 54
Safety devices
· Front emergency bar
· Infeed pressure roller with overthickness and anti-kickback system
· Disc brake on each unit for EMERGENCY STOP
· Front and rear emergency pushbuttons
Emergency STOP
· Sanding belt breakage
· Sanding belt not in tension
· Sanding belt running out
· Low compressed air pressure
· Sanding belts and conveyor motor overload
· Door opening (bypassed with key-selector)
· Front machine overthickness detector
Pneumatic system
· Padlockable compressed air cutout valve
· Air filter with condensation separator with automatic drain
· Self lubricating system for pneumatic components
Sanding drums
· Made of steel, mounted on eccentric Shaft, to adjust the sanding belt thickness
· Drum rubbered with helicoidal grooves, balanced and rectified
· Dust captation hoods with special design for best performance
· Pneumatic ON/OFF of unit from panel control
· Sanding belt tension rollers made of steel, balanced.and rectified
· Front pressure rubberised roller (1 roller)
· Back pressure rubberised roller (1 roller)
Conveyor
· Worktable made of machined steel
· Worktable lifting system with four large diameter trapezoidal screws
· Worktable motor-driven adjustment
· 60Sh rubber conveyor belt with ground laminar surface
Pneumatic conveyor belt tracking
· Front table extension: 1 (one) roller powered
· Rear table extension : 1 (one) roller powered
General machine devices
|
Working width: 1350 mm |
|
|
Machine constant pass line TM (fix table) |
|
|
Acoustic material |
|
|
Working height 200 mm |
|
|
Laser electronic positioning for working thickness measuring |
|
SPVE00010 |
Electric execution UL/CSA approved |
|
SPVE00015 |
LED lighting inside the machine |
|
PHTE400 |
Voltage 460/60Hz |
|
SDAG00038 |
Reading bar electronic pad 42 sections |
|
|
Electronic longitudinal sanding belts tracking
|
|
1st Working Unit
SPVS00001 |
Spinbrush unit Unit is composed by 11 rotating brushes, with cross oscillation. Unit Spin Brush 11 (Viet patent 2005) allows operation on raw and/or varnished panels, "trimming" the edges. On raw panels is the ideal solution because all edges, front/back panel and also on inside edges of frames, are trimmed perfectly and uniformly. In the varnished panels action is absolutely correct, trimming perimetral and inside edges, cutting the sharp edge left by lacquer. The unit works taking advantage of the 3 different movements (two different senses of rotations and one cross oscillation) of the abrasive fingers, considered the panel surface, and guarantees uniform sanding process all over the panel surface. Oscillation of unit is guarantee by a double slide bar with ball recycle system. "Quick Change System", with "spring reaction" for "flats" changes. The 11 "flats" mounted in the housing, are entirely produced at Viet Factory and design/ solution has been patented. On each element "flat" can be installed any kind of "tool" as abrasive stripes produced expressly on customer's demand, based on applications. The group has an independent electronic working height regulation, to set the interference. Setting the "interference" of abrasive stips on panel, the "flats" speed and oscillation, allow to combine the aggresiveness of abrasives and the finish obtained is uniform. Spin Brush 11 unit is delivered with 1 set of "flats". For to have a quick change when in need to replace the used abrasives, we suggest to buy an extra set of ?flats?. This gives to customer the possibility to configurate/replace units, without waste time, having a spare set. For to furthermore help operator in saving time when changing units, the entire "castle" where Spin Brush 11 is installed, slides out of the machine body, left side |
. |
SPAG00005 |
132 Abrasive inserts gr.240 (11 for each disc) |
|
SPAG00008 |
132 brush inserts (11 for each disc) |
|
SPAG00009 |
n› 11 additional abrasive disks (extra set) |
|
SPAG00005 |
132 Abrasive inserts gr.240 (11 Extra) |
|
SPAG00008 |
132 brush inserts (11 Extra) |
|
SPVG00011 |
Electronic inverter 11kW (15HP) |
|
2nd Working unit
SPVL00007 |
Working unit for housing a 36 strips roller brush diameter 300 mm |
. |
SPVL00025 |
Brush unit: aluminium hub 36 slots |
|
SPAG00015 |
Brush inserts (18 inserts) |
|
SPAG00018 |
Abrasive inserts gr.240 (36 inserts) |
|
SPAG00036 |
Oscillating system |
|
SPVG00008 |
Electronic inverter 4kW (5,5HP) |
|
SPIV00001 |
Reverse rotation sanding belt |
|
3rd Working Unit
SPVL00007 |
Working unit for housing a 36 strips roller brush diameter 300 mm |
. |
SPVL00025 |
Brush unit: aluminium hub 36 strips (no strips included) |
|
SPAG00015 |
Brush inserts (18 inserts) |
|
SPAG00018 |
Abrasive inserts gr.240 (36 inserts) |
|
SPAG00036 |
Oscillating system |
|
SPVG00008 |
Electronic inverter 4kW (5,5HP) |
|
SPIV00001 |
Reverse rotation sanding belt
|
|
4th Working unit
SPVT00017 |
Superfinishing unit - 2620 for housing a sanding pad The super-finishing pad is the evolution of the pad unit (Viet patent, 1978). The pad unit has a "chevron belt" running between the pad itself and the abrasive belt that guarantees top-quality finishing and a longer performance to the abrasive. |
. |
SPVT00004 |
HP Electronic segmented pad 42 sectors (32 mm pitch) The segmented electronic pad allows sanding at a high quality level thanks to the electro-pneumatic sectors activated only by the surface of the panel. |
|
SPLM00007 |
Sliced contact insert made of steel + felt for HP |
|
SPLM00008 |
Narrow sliced contact insert made of steel + felt for HP |
|
SPLM00009 |
Removable graphite cloth |
|
SPAG00065 |
Electronic pressure setting for electronic segmented pad |
|
SPVG00012 |
Electronic inverter 15kW (20HP) |
|
SPSF00001 |
Linear blower cleaning sanding paper A.S.S. (Air Saving System) |
. |
Additional Units
|
Standard outfeed belt prepared for the combination of one group brush and a cleaning accessory |
|
Conveyor
SPVA00005 |
Electronic inverter 2,2kW (3HP) |
|
SPDP00006 |
Vacuum table complete with 1 fan of 5,5kW - 7,5HP with electronic system for regulating the flow |
. |
SPVA00008 |
40SH rubber hardness conveyor belt with profile |
|
SPAA00001 |
Front table extension 2 (two) rollers |
|
SPAA00002 |
Rear table extension 2 (two) rollers |
|
Main drive panel
|
IPC COMPACT 8,5' The COMPACT Touch Screen control panel offers the complete management of machines consisting of a maximum of 4 units, including accessories present in the machine. The intuitive graphics and simple setting make it suitable for all types of machines configuration. |
. |
Additional Options Included
SPAG00037 Motorized height adjustment system for brush- 2nd unit
SPAG00037 Motorized height adjustment system for brush – 3rd unit
The listed specifications & information were taken from the manufacturer’s published information, internet research, or seller’s description.
The specifications & information are assumed to be correct; however, in no way, guaranteed. Bidders are encouraged to inspect the machine, call with questions, or contact the manufacturer for more information.
Please log in to view the bid history
LoginNo information available