Homag yr 2020 "Centateq N-300" Machining Center - 5x10 table, (2) Vac Pumps
Ended
Aeonic Kitchens 6606Line 87 Listowel, ON Canada N4M 3G6
- Winning Bid : $104,652.00 USD Sold
- 157 Bid(s)
- High Bidder: j****a
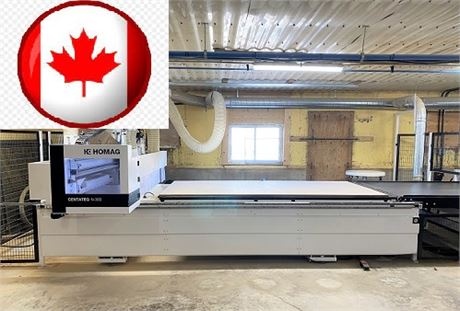
Homag Centateq yr 2020, Felder 24" Planer, SawStop, Sander in ON Canada ( Closed #45808508 )
Aeonic Kitchens Located 90 MInutes North of Toronto is Downsizing and Offering up for Bid Recently Purchased (Low Hour) Machines in Ex. Condition Including Homag Centateq N300 CNC machine yr 2020 * SawStop 10" Table Saw * Felder 24" Planer * Weeke Widebelt Sander and much more...
-
Pick Up Location
Aeonic Kitchens 6606Line 87 Listowel, ON N4M 3G6
-
Make
Homag - LESS THAN 450 HRS
-
Model
Centateq N-300 c/w Homag Woodwop Software
-
Serial Number
250-69-0973
-
Year
2020
-
Phase
3 PHASE
-
Voltage
480 VOLT
-
Load Out Period
Mar 16 2023
-
Estimated Dimensions
Coming Soon
-
Estimated Weight
9,000 lbs
-
Seller Comment
-
Load Fee
4500
-
page views
3719
Homag Centateq N-300 CNC Machine
c/w Safety Gate, Tooling & Extras as seen in Photos
HSK 63 Router Spindle Power 10 kW (13.4 HP)
Router Spindle Speed 1,250-24000rpm
Tool Magazine Capacity 7*
Pnuematic Reference 11
Working Length 10'
Working Width 5'
Maximum Workpiece Thickness 100mm
X/Y/Z Vector Speed 96/96/25 m/min
Z Stroke 9.6"
CENTATEQ Series machining centers help customers worldwide increase productivity, reduce errors, and lower cost of ownership. Rigid, fast, and reliable, each unit is constructed with an extremely durable foundation to accommodate the router's high-speed capabilities while ensuring the machine's accuracy and longevity. With numerous automated features and intuitive touch-screen controls, the CENTATEQ Series is easy to learn and operate.
Features & Details:
HOMAG CENTATEQ N-300
HOMAG drilling technology is top of the line
-
Ball bearing arrangement provides for the compensation of forces from all sides and delivers the highest drilling quality. The more demanding the application, the more important this feature is.
-
Thecleverarrangementofthedrillspindleensuresaconstantdistancebetweenthedrill bit and the bearing, whether the spindle is extended or not. Together with the diameter of the sleeve, this feature ensures the highest lateral stability and precision during the drilling process.
-
IntegratedMechanicalClampingSystemtoensureeachdrillspindleachievesproper depth regardless of material density and/or drill diameter
-
Structural Composition
-
Singlepiecesteelframeweldment
-
Singlepiece,spanreinforcedsteelgantryweldment
-
Vibrationdampeningcast-aluminumZ-plate
-
1.5”structuralplatesteelforleveling,pairedwithstructuralhorseshoecollarsforsecuring machine to the foundation
-
LevellingsystemdesignedtoincorporateISOLOCVibrationEngineering
• Providesforasecurefootingwith5-degreecompensationforlessthanperfectfloors • Providesforinsulationandreductionofstructurebornenoise
-
Guide System and Drive Technique: Precise, accurate, consistent
The X, Y, and Z axes are all supported on THK-style linear motion guides. These guides are engineered to produce straight line tracking at high travel speeds while providing stability in both the radial and lateral directions.
• The X axis is driven by two (2) helically-ground rack and pinion gear systems • TheYandZaxesaredrivenbyhigh-precisionballscrew
• SolidstatedrivesanddigitalACservomotorspowertheaxes
• DigitaldrivetechniqueinX,YandZdirectionfeatures:
• Maintenance-free motors with high-resolution optical encoders for precision and accuracy
• Digital drive control units guarantee high reliability
MATRIX Table 5′ x 10′
A grooved phenolic MATRIX vacuum system is standard. It clamps down work pieces on the
table surface. The grooves allow efficient vacuum distribution; they also isolate table areas by inlaying a rubber seal and/or by accepting vacuum pods to affix small parts. Rubber gasket material is included.
• Workpiece thickness:maximum100mm (3.94Inches)
PRO+ Matrix Table: Minimal set-up time means more productivity
The PRO+ solution is designed to handle the variety of raw material needed by multi-faceted manufacturers.
Vacuum System: Reduces risks for peace of mind
Vacuum systems, which hold down material while cutting, use more electricity than any other machine function. The CENTATEQ system uses an eco-friendly design to conserve energy and utility costs.
• Includes 2 vacuum pumps
• See Photos
Energy Saving
On-demand vacuum
The machine carries the ability to monitor vacuum pressure and automatically call pumps into
action to maintain minimum vacuum pressure. This feature is a useful costs savings tool for
those customers operating in areas where electricity during peak hours is costly. For those not
wanting to employ the feature, it can simply be deactivated.
Stand-by operation
To save energy, the machine’s ecoPlus button can be activated to start stand-by operation after a pre-set time while the machine is not processing.
• Primary power of drives is switched off
• Vacuum pumps are switched off
• Setsapotential-freeoutputthatcanactivatetheslide(suppliedbythecustomer)ofan external extraction device
Top performance and environmental responsibility
Multi-Zone Processing
The table and control interface on the CENTATEQ Series allow the operator to simultaneously load multiple programs at up to 4 zero points (number of zero points determined during machine specification). The machine then optimizes drilling and routing routines and runs the multiple programs as a single file. This is an important feature for those who may use the CENTATEQ Series machine as a “point to point” machining center or provide back-up to that style machine already in operation on their shop floor. An example of this in production is an operator loading smaller raw materials to the machines multiple reference points and running the parts in a single optimized machine cycle.
Vertical Router Spindle: Adding long-term value
The BENZ/ZIMMER GROUP HSK63 spindle motor is rated at 18 HP, but the machine operates it at a maximum capacity of 13.4 HP. This output meets virtually all application needs, reduces energy costs, and increases longevity.
-
Includesanautomatictoolchangefeaturewiththetoolchangemagazine
-
Directionofrotation:righthand/lefthand
-
Speed: 1,500 - 24,000 rpm stepless programmable
-
Drive:frequencycontrolledtoamaximumcapacityatthetool:upto8.5/10kW(11.4/13.4 HP) in continuous and intermittent operation (S1/S6 - 50%)
-
Spindlelubrication:permanentgrease
-
Bearing:hybridbearing(ceramic)withlittlefriction,higherstiffness,andmaximum operating life
-
Fancooled
-
Centraldustextraction
-
Air Jet
Four flexible air jets are integrated into the extraction hood, providing a cool, clean, and efficient machining area. Air jets are activated via soft key at the control panel.
Automatic Tool Changer: Eliminates human error
To increase flexibility and decrease cycle time, an automatic tool changer (ATC) is located near the left of the machine framework.
• Toolholder:HSK63
• 12 toolplacesintoolmagazine
• Toolweight:maximum5kg(11.02lbs.)includingHSKcone • Tooldiameter:135mmmaxwhenequippedwith7tools
• Toolchangetime:approximately10-18seconds
• Toolloading:viaintegratedpick-upplaceatthetool
Automatic Tool Changer Loading Position
From a single position, operators can easily and quickly insert and remove tools.
Tools are manually inserted into the loading device, positioned close to the left front of the machine for easy access. The machine retrieves the tool and selects the first available position in the tool magazine, deposits the tool, and updates the tool database.
To remove tools, the machine deposits tools in the loading position and automatically removes the tool from the active tool database. Sensors prevent the machine from depositing a tool when another tool is present.
Tool Length Control
A heavy duty tool length control system is a standard feature. To maintain accuracy, the machine measures the length of the tool and verifies it against the tool data stored in the machine control. This reduces human error, eliminates the need for multiple test cuts, and saves set-up time.
7-Spindle Vertical Drill Block: Precise, accurate, and consistent
Drill blocks increase the processing speed of the machine by allowing drilling operations to be accomplished without changing tools. Spindles in the drill block can be selected individually to meet different needs simultaneously.
• Spindleclampingachievesprecisedrillingdepth
• StrokeZ-direction:60mm
• Drillingdepth:maximum38mm(upto55mmforspecialborers) • Directionofrotation:righthand/lefthand
• Speed:3,450rpm
• Power:1.5kW
• Shaftdiameter:10mm
• Totallengthofdrill:70mm
• Drillingdiameter:maximum35mm
• Distancebetweenspindles:32mm
• Typeofspindle:individuallyselectable
• Spindleconfiguration:4X–3Y
Pneumatic Side Reference Fences and Locating Pins: More flexibility, less risk of failure
Pins and fences are automatically actuated and surveyed by the machine control to prevent operation when the pins are not completely depressed.
To supplement pneumatic reference pins, full-length solid fences help position materials in the working zones of the machine. Paired with pneumatic reference pins located at the front right and front left of the machine, the system offers two “zero” points for accurately locating raw materials. Fences retract during machining. When the finished nest is ejected, the fences are raised again to help guide parts from the machine table to the transfer conveyor at the end of the machine. Both the fences and the pins are under down stroke surveillance to prevent the machine from routing a fence or pin in the event of an incomplete cycle.
Push Off Material Handling Package: Enhances return on investment
The Push Off material handling system can increase output by as much as 40% over a standard manually off-loaded machine, while continuing to require only one operator. The increase can be achieved without adding labor, running a second shift, or purchasing another machine.
Automated Push-Off of Finished Nests
The system utilizes a gantry mounted push-off device to automatically eject finished parts from the machine table onto a transfer conveyor without manual operator intervention. Once the nest is complete, the gantry returns to the loading side of the machine, drops its push-off device, and cycles from left to right, collecting finished parts and waste along the way. A table cleaning sweep is integrated into the push-off to clean dust and debris from the spoil board in preparation for the next raw board.
Transfer Conveyor
A conveyor belt receives the finished parts and automatically advances them to the operator for sorting at the end of the table via communication with photo-electric sensors. This allows more efficient operation because the machine can process parts while the operator unloads the previous nest. It also prevents parts from being pushed off onto the floor if the operator is not present to receive them. Minimum recommended part thickness for consistent part conveyance is 12mm (1/2”).
Pneumatic Side Reference Fences and Locating Pins
To supplement pneumatic reference pins, full-length solid fences help position materials in the working zones of the machine. Paired with pneumatic reference pins located at the front right and rear right of the machine, the system offers two “zero” points for accurately locating raw materials. Fences retract during machining. When the finished nest is ejected, the fences are raised again to help guide parts from the machine table to the transfer conveyor at the end of the machine. Both the fences and the pins are under down stroke surveillance to prevent the machine from routing a fence or pin in the event of an incomplete cycle.
Dust Extraction from Below
The dust extraction from below collects dust that remains in the cut line as the parts are pushed off the machine. This system also has an integrated blast gate to concentrate dust collection volume to this area of the machine when it is needed. This results in less cleaning at the end of a shift.
Dust Collection from Above
The transfer table has an integrated dust collection hood from above to clean residual dust from the tops of work pieces and the conveyor belt. As a result, parts are free from much of the dust and debris of the machining process. This proves very valuable for those applying barcode labels or other methods of identifying parts coming from the router.
480V c/w transformer to 600V for cdn Buyers
LOAD FEE: Call us (416) 904-2475
Listed specifications were taken from manufacturer's published information and is assumed to be correct but not guaranteed. Bidder is encouraged to inspect the machine, call with questions or contact the manufacturer for more information.
The listed specifications & information were taken from the manufacturer’s published information, internet research, or seller’s description.
The specifications & information are assumed to be correct; however, in no way, guaranteed. Bidders are encouraged to inspect the machine, call with questions, or contact the manufacturer for more information.
Please log in to view the bid history
LoginUS & CDN CUSTOMS BROKER
Cole International (905) 672-6255
US BUYERS SHIPPING QUOTES:
Always Trucking (Aaron) 541-608-6532
SHIPPING WITHIN CANADA QUOTES;
Logistics Decisions (Adam) (905 -331-8900
LOCAL FLAT BED TRUCKING QUOTES:
Affordable Trucking (Youseff) 416-820-2033
RIGGING QUOTES IF LOAD FEES NOT LISTED:
Turn Key Industrial (Tony) 416-993-6380
No information available
CDN FUNDS: This Auction is Being held in CDN Funds.
PAYMENT: Is Required Within 48 hrs of Auction Ending.
PAYABLE METHOD: To Equipment Authority
REMOVAL: At Buyers Expense
REMOVAL DEADLINE: Mar 16, 2023
INSPECTION DATE: By Appointment
AUCTION END DATE: Wed Mar 08 2023 at 1:00 pm EDT
BUYER PREMIUM: 15% Buyer Premium Sur Charge Will Be Added to All Lots