(2017) Stefani "Solution HD" Edgebander - PUR, Grooving Saw, Pre-Mill & Crnr RD
Ended
Windsor Fixtures -Complete Plant Closure -Day 1- Lawrenceville, Ga
- Winning Bid : $183,300.00 USD Sold
- 185 Bid(s)
- High Bidder: S****c
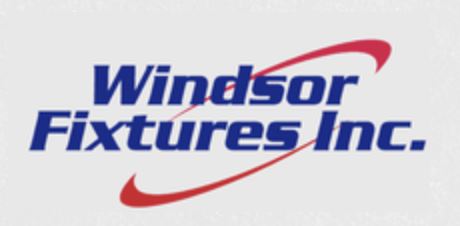
WINDSOR FIXTURES INC COMPLETE PLANT CLOSURE - LAWRENCEVILLE, GA - DAY 1 ( Closed #26329166 )
For Rigging/Loading please contact:
Gorham Industrial, LLC - James Gorham - 803-617-8434 - [email protected] - www.gorhamindustrial.com
Preston Machinery, LLC - Tom Preston - 269-685-7591 - [email protected] - www.prestonmachineryllc.com
For Shipping Quotes, please contact: NCL Trucking, John, 615-452-7651
-
Pick Up Location
755 Raco Dr, Lawrenceville, GA 30046
-
Make
Stefani
-
Model
Solution HD
-
Serial Number
AH/006249
-
Year
2017
-
Phase
3 PHASE
-
Voltage
208-230/460
-
Load Out Period
April 9, 2020
-
Estimated Dimensions
30'x5'x71"
-
Estimated Weight
4,400 Kg
-
Seller Comment
CONTACT ALWAYS TRUCKING for shipping quote 541-608-6532
-
Load Fee
A rigger is required for this lot. Gorham Industrial, LLC 803-617-8434 [email protected] or Preston Machinery, 269.685.7591, Tom Preston, [email protected]
-
page views
4632
In light of how many Edge Banders are in this auction, we want to be clear about what options each has. The specs below are a general guideline but verification of anything specific may be verified in person at the provided open houses. You may also choose to e-mail the Shop Engineer, Steve Hardy: [email protected]
Heavy-duty automatic edge bander
The dust extraction manifold as shown in the pictures is included. It includes the pipe that would encompass the machine and flex hoses. It does not include the remaining pipes to the dust collector.
SOLUTION HD |
MAIN FEATURES
|
"E TOUCH" CONTROL WITH AUTOMATIC PROGRAMMING: JUST A “TOUCH” FOR USING THE MACHINE |
|
PRESSURE BEAM WITH BELT AVAILABLE AS STANDARD FOR THE BEST PANEL HOLDING |
|
GLUING FOR APPLICATION OF EDGE IN COILS, STRIPS AND SOLID WOOD |
GENERAL FEATURES
Automatic single-sided edge bander for the edge gluing with hot melt glue, equipped for panel edge banding with material in coil or strips. Fixed working side on the left.
The machine base is made of a high rigidity single steel block giving optimum support for the working units.
The top pressure beam is made of thick steel with a twin-profile V-belt and automatic positioning according to the panel thickness by NC.
Height adjustment visualised by means of mechanical indicator and on the operator console.
Manual infeed panel system with widely dimensioned guide and enlarged support surface to make the feeding operations of even large panels easy.
Adjustable infeed guide on two positions
for automatic selection of the working process with or without the pre-milling unit.
Top operating groups fixed to the pressure beam or mechanically connected on to it to allow automatic positioning according to the panel thickness. Lower groups fixed to the base or the horizontal beam for a precise reference with respect to the panel.
All high frequency motors are equipped with static inverter.
Inverter for each operating unit equipped with motor, in order to optimise the flexibility and the production times of the machine
Safety enclosure on all units installed after the gluing unit.
The enclosure doors have wide poly-carbonate windows for the groups visualisation during machining.
Safety enclosure lined with soundproofing material, complete with lamps for internal lighting of the gluing and machining zone.
Panel spacer,
positioned on machine infeed to allow the panels loading into machine with the right space between them. Automatic change of the loading distance according to the selected working speed.
Exhaust outlets for the operating groups positioned on the top side of the safety enclosure.
Mobile control panel at machine infeed for an easy use from the operator''s working position.
Electrical cabinet in conformity with the current safety regulations.
Electrical components positioned inside the metal case, fixed to the machine base with door that allow an easy access in case of any maintenance operations.
Feed track made of 80 mm wide nylon pads, coated with wear proof vulcanised rubber with a high coefficient of friction to grant an optimal panel holding and a high machining precision
Sliding of pads on two guideways (in hardened and ground steel), one round and one flat, to ensure straightness of movement and resistance to side loads.
Automatic pads lubrication.
The oil quantity is optimised by the machine control according to the machined panels.
Panel support rollers positioned parallel to the track. It can be extended on the entire length of the machine. It is made of telescopic opening system with 650 mm extension (for panel with 1200 mm maximum width).
E-TOUCH
PC control system for fast and easy handling of the main machine functions.
It foresees:
- Creation of “Just in Time” programs.
- Possibility of management by means of a production list.
- Possibility of management by means of a Bar Code Reader (option)
- Flexible program change: the selection of the new working program does not require the “free of panels” machine. The machine optimises the distance between panels automatically selecting the necessary space to carry out the set up.
- Possibility of handling with “SIDE FINDER” application which facilitates the operator to identify the exact panel side to be introduced.
- Virtual preview of the processed panel with automatic selection of operating units
- 3D virtual preview of the processed panel with automatic selection of operating units
- Working units ON/OFF control
- Clear and guided diagnostic information for fast resolution of any problems
- Working statistical data: number of worked pieces and meters, employed hours used
- Management for automatic and immediate selection of the edge coil (when the multi-coil magazine is present)
- Rapid selection of all main functions from the main page
- Unit of measurement in mm
- Operator interface in the following languages: Italian, French, English, Spanish, German (Portuguese and Russian are optional).
- Unlimited number of working programs.
- Programming of turning on the glue pot, for the timed switch-on of the pre-heating unit inside the glue tank
PC Office main features.
Operating system: Windows 7 Professional.
Screen: 17" TFT LCD Touch screen.
2 ETHERNET network card.
6 USB ports - 2 ps/2 ports and possibility of connection for Bar Code reader management, DVD reader.
Remote diagnostics web / based allows connection via Internet of the machine PC supervisor to SCM Group Service.
Software equipment:
TEAMVIEWER® .
Software for remote diagnostic control of the machine via internet
Furthermore it allows
- view of operator interface
- signal diagnostic
- on-line checking and editing of the configuration, parameter and program status of the machine
- data backup and file transfer
- upgrade of the machine logic and operator interface
Preparation of internet access on the machine PC is at customer's charge
KASPERSKY® Internet Security
PC's are equipped with antivirus protection software and Kaspersky Internet Securit firewall.
The license has a term of one year, starting from the despatch date of the machine.
The licence renewal at maturity is at the customer's charge. If not renewed, the product is not deactivated, but it becomes impossible to update it with new virus definitions.
SAFETY REGULATIONS
The machine is in conformity with the following directives:
- Directive 2006/42/CE ("machine")
- Directive 2014/30/UE ("electromagnetic compatibility")
Enclosed user manual
Standard paint finish: Grey RAL 9002
Note:
The performance indicated in the offer can vary according to the type of machining
(especially according to the speed, processed materials and material removal to be carried out)
A0.00.76 |
Solution HD - "HD-RT4" composition (78) |
N. 1 |
|
NOTE
The machine includes the free space for the installation of the following optional groups:
(1) = Spindle moulder or Sanding unit
(½) = Glue scraping unit
(1F) = Hot air blower
TECHNICAL DATA
GENERAL FEATURES |
||
Variable track feed speed |
m/min |
10 - 25 |
Panel thickness |
mm |
10 – 45 (opt. 60) |
Thickness of coiled edge |
mm |
0.3 – 3 |
Thickness of edge in strips * (with option: “kit for solid wood up to 22 mm”) (option not available for A-B compositions) |
mm |
0.3 - 12 (opt. 22)* |
25 m/min distance between two successive panels (according to the selected units) |
mm |
600 |
Minimum panel length with edge in coils |
mm
|
145
|
Minimum panel length with solid wood edge - without counter shoulder |
mm mm |
200 380 |
Minimum panel width (250mm minimum length) |
mm |
95 |
Work table height |
mm |
950-970 |
Electrical supply |
|
Three-phase+neutral |
The composition includes the following units:
"RT-E" pre-milling unit
it trims the panel edge obtaining a perfect uniform surface for the glue application and a perfect jointing line with the edge.
The unit is equipped with:
-
- two high frequency motors. Motor operation is timed to prevent chipping on the panel
- exhaust hoods
- timed air blower for the cleaning of the machined panel surface
- panel edge trimming with a variable removal, adjusting the infeed fence position by means of knob and numerical readout .
- height adjustment of the motors to vary the cutters working point
- infeed fence with two automatic positions to work with or without the unit
- complete with no. 2 “ED-SYSTEM” diamond tools D=100 H=49 Z=3+3
Max. removal |
mm² |
90 |
Max thickness removal |
mm |
3 |
Motors power |
kW |
4 |
Tool height |
mm |
49 (opt. 63) |
Tool rotating speed |
rpm |
9.000 |
Maximum working speed |
m/min |
30 |
"VC600-12/QMS" gluing unit
For the gluing on straight profiles of edges in coils and in strips with hot melt glue spreaded on the panel:
Glue pot:
- interchangeable glue pot with manual release device with teflon anti-adherent treatment to avoid incrustation
- glue level check through reflection photocell.
- fast glue pot interchangeability
- device to measure out the glue
- automatic control of the glue temperature
- automatic exclusion
- handling of the glue spreading roller, of the first pressure roller and of the feed roller by motors
- automatic lowering of the temperature, to avoid the glue overheating in case of a temporary non-use of the machine (especially for a momentary interruption of production)
- “ iGlue” device which includes:
* automatic locking of glue pot copying operation in the
last panel sections; it avoids a glue excess quantity on
the panel rear side
* automatic glue pot exclusion
QMS pre-melting unit
it automatically supplies the glue pot that is already at the working temperature.
Manual control for unloading the glue in case of the substitution of the type of glue being used
Edge loading
- sash-shear device for coiled edges
- automatic edge loading system for material in coils and strips which allows to change the type of the applied edge in a short time
- 3 interchangeable feed rollers: needle roller for solid wood and knurled roller for thin and plastic edges, rubber roller for delicate edges
Edge pressure roller
- pressure area with independent pressure adjustment
- the first roller of large dimensions (150 mm) is powered with clutch and made of teflon
- three idle rollers with opposed conicity and timed intervention with 75 mm diameter.
- mechanical position indicator
horizontal coil-holder plate
- plate for 1 coil with 800 mm maximum diameter and manual loading
Glue pot installed power |
kW |
2.6 |
Glue pot heating time |
min |
15 |
Glue pot capacity (with QMS pre-melting unit) |
Kg |
0.5 |
Capacity of pile-form in strips |
mm |
220 |
Minimum length of edge in coils |
mm |
250 |
Minimum length of edge in strips |
mm |
250 |
Maximum section of edge in coils |
mm² |
135 |
Exceeding material to the panel thickness |
mm |
2 + 2 |
Maximum working speed |
m/min |
25 |
"YU/SP-750" upper end cutting unit
It carries out the cutting of the front and rear exceeding edge (also for post/soft formed panels).
- The unit is fixed to the top presser
- 2 high frequency motors
- 0-15° independent automatic blades tilting (front/rear)
- horizontal motor sliding on round and ground bars
- side and front copying device for an accurate positioning of blades in relation to the cutting point
- automatic exclusion of the side copying devices
- complete with cutters
Motors power |
kW |
0.55 |
Speed of cutters |
rpm |
12.000 |
Max. section to be selected |
mm² |
1300 |
Automatic horizontal exclusion |
mm |
25 |
Installed tools |
no. |
2 blades Ø150mm |
Maximum working speed |
m/min |
25 |
“R” in-line trimming unit
For the rough trimming of thin and medium edges or for the finishing of the solid wood edge:
- two overlapped motors provided with quick release
- top motor connected to the pressure beam for the automatic adjustment according to the panel thickness
- vertical copying discs of large diameter
- numerical indicators for the horizontal and vertical motors movement
- automatic exclusion.
- two automatic positions for the rough trimming of thin and medium edge and for the finishing of solid wood edge
- complete with tools
Motors power |
kW |
1 |
Speed of cutters |
rpm |
12.000 |
Minimum panel thickness |
mm |
10 |
Installed tools |
|
straight cutters |
Maximum working speed |
m/min |
30 |
“RSU” tiltable chamfering unit
For the finishing of thin or wood edges or for the rough trimming of the radius on ABS/PVC edges:
- top motor connected to the pressure beam for the automatic adjustment according to the panel thickness
- vertical copying discs of large diameter
- lateral copying discs with independent horizontal adjustment
- numerical indicators for the horizontal movement of motors and copying discs
- independent pneumatic exclusion of the unit (upper/lower)
- complete with tools for straight machining
- quick release motor kit for R=2 machining
Motors power |
kW |
0.5 |
Tools rotating speed |
rpm |
12.000 |
Minimum panel thickness with radius |
mm |
10 |
Manual motor tilting |
|
0-30° |
Installed tools |
no. |
2 heads for straight |
Maximum working speed |
m/min |
30 |
"C1+C2" rounding unit
to carry out the front and rear rounding on the transversal side of shaped panels or on PVC/ABS edges and thin solid wood with a very high degree of finishing quality:
- four motors provided with quick release system with motor block + tool supported by a parallelogram kinematic motion which allows the unit to follow the head (end) of the panel in sequence, independently from the geometry of the profile
- “ED-System ” high efficiency exhaust hoods and tools
- separate processing sequences to avoid the simultaneous working which could cause vibrations of the panel, provided with oscillating motion to follow the panel;
- copying system made of copying discs and lateral copying device
- automatic exclusion
- complete with tools for R=2 machining
Motors power |
kW |
No. 4 – 0,35 |
Speed of cutters |
rpm |
12.000 |
Edge thickness |
mm |
0,3 - 5 |
Pabek thickness |
mm |
10-60 |
Minimum panel length:
|
mm mm mm |
170 180 220 |
Maximum working speed when rounding |
m/min |
22 |
Centre-to-centre distance between panels
|
mm mm mm |
500 525 550 |
"RCS" edge scraping unit
For the finishing of radiused PVC/ABS edges:
- quick release device made of a tool-holder block + tool which allows the fast and precise changing of the tool
- vertical and horizontal shifting devices made of steel grounded bars with recirculating ball bearings
- vertical and horizontal copying devices with large diameter
- suitable cleaning and spray-mist blowers for each tool
- suction of the edging cuts-off with suitable container for chips
- numerical indicators for the horizontal movement
- horizontal independent automatic exclusion
- complete with tools for R=2 machining
Minimum panel thickness with radius |
mm |
10 |
Vertical/front copying devices |
|
disc/disc |
Maximum working speed |
m/min |
30 |
"SPE" brushing unit
for the cleaning and finishing (polishing) of plastic edges:
- two overlapped motors complete with two cloth brushes
- vertical positions of motors, manually adjustable by means of a knob
- motor directly connected to the pressure beam for the automatic adjustment according to the panel thickness
- manual exclusion
Brushes positioning:
- 10 degrees horizontal tilting
- 4 degrees maximum vertical tilting
Motors power |
kW |
0.25 |
Rotating speed |
rpm |
1500 |
Diameter/thickness |
mm |
160/25 |
A0.01.04 |
NR. 1 USE AND MAINTENANCE HANDBOOK IN ENGLISH -GB- |
N. 1 |
|
99.00.61 |
PC ENGLISH LANGUAGE |
N. 1 |
|
A0.01.91 |
ELECTRICAL SCHEME IN ENGLISH |
N. 1 |
|
93.07.36 |
Volt 380 |
N. 1 |
|
93.15.01 |
Frequency 60 hz |
N. 1 |
|
A0.00.72 |
UL/CSA version |
N. 1 |
|
B0.00.02 |
Autotransformer kVA 75 V208-230-460 conf.UL/CSA |
N. 1 |
|
A0.02.81 |
No.2 panel heating lamps |
N. 1 |
|
set before the gluing unit to pre-heat the side of the panel before glue application.
A0.00.27 |
Edge detecting sensor |
N. 1 |
|
It is suggested for the automatic loading of thin edges in strips (i.e. veneered panels)
A0.02.76 |
Electronic positioning of pressure rollers |
N. 1 |
|
Positioning of the pressure roller-conveyor by numerical control to set the position at the edge thickness changeover.
A0.02.92 |
Anti-adhesive device for first pressure roller |
N. 1 |
|
A0.05.03 |
"SGP" glue pot in substitution of the standard one |
N. 1 |
|
It allows a quick changeover of the used glue type/colour. The glue pot is fed by the standard pre-melting system for EVA glue.
Features:
- specific compact design that reduces to a minimum the melted glue before the application in order to maintain the best quality characteristics.
- anti-adherent treatment for EVA or PU glue.
- spreading roller with optimized graining and PLASMA anti-adherent treatment
- manual emptying cycle with collection of the residual glue on a removable tank
- automatic locking of glue loss with stopped machine (SCM GROUP patent)
- manual dosing adjustment with graduated indicator
- glue roller reverse rotation
- quick release device for the removal and easy replacement of the glue pot
- simple and quick access for the internal cleaning with the possibility to disassemble all parts.
- short time of heating of the glue during the starting of the machine thanks to its small dimensions
- double thermo-regulation system for an easy use of two types of glue with different melting
Technical data:
heating time from environment T°: <10 min
heating time from pre-heating T°: <5min
glue capacity: 0,5 Kg
installed power: 2,05 kW
A0.03.17 |
"PUR BLUE 4 HO" PU glue premelter for "EB 60" slot + "EB 60" PU glue slot applicator |
N. 1 |
|
Melt On Demand pre-melting process for PU glue
The glue cartridge (which can be inserted in the melting box with the protective film) through a pneumatic pusher, is pushed on a heated grill, that melts only the first glue layer.
The device is equipped with operator interface on pre-melting board and interface with the main edge banding control
The cartridge can be removed without damage after a partial use, as it is not fully melted.
Electronic temperature control. Under-/over-temperature monitoring.
Pump with variable rotating speed to adjust the glue capacity supplied directly from the control interface.
0.5 Kg melted glue stock under the melting box area. It allows sufficient duration to substitute the ended cartridge without stopping the machine time
Heated hose which allows the melted glue supply up to the EB 60 applicator. Reinforced Inox steel, thermo-isolated hose, with disconnect fittings for the connection. FE/KO thermo-couples.
PU EB 60 application unit
Spread test for gluing edges with polyurethane glues. Spread width can be easily modified by rotating a manual control handwheel. A special graduated scale enables the spread width to be precisely identified.
Technical data
- Melt capacity: 6 kg/h
- Operating temperature: °C 50-150
A0.02.85 |
Independent exclusion for "YU" motors |
N. 1 |
|
For the processing of non-orthogonal panels (ex. a triangle) or every time the end trimming on only one side is required.
A0.00.90 |
Air blower for panel cleaning |
N. 1 |
|
A0.05.47 |
Exhaust hoods with teflon treatment in place of the standard ones on the "R" trimming unit |
N. 1 |
|
A0.01.46 |
1,8 kW motors instead of the standard ones ( RSU UNIT ) |
N. 1 |
|
A0.01.47 |
2 pneumatic positions kit with electronic positioning of copying devices for "RSU" chamfering unit |
N. 1 |
|
Device for the automatic tool positioning from control panel for a rapid working change-over according to the applied edge thickness (from thin edge to 2 mm and vice-versa) with management of the different thin edge thickness from control panel.
It replaces the “RSU” manual unit complete with straight cutters and 2 motors kit with R=2mm cutters included in the standard composition with the 2 automatic positions “RSU” unit with axes on side copying devices.
It includes:
- motors with 2 positions vertical and horizontal automatic positioning
- side copying discs with integrated horizontal electronic positioning
- Installed tools (in place of the standard ones) : Widia type with throwaways knives: Ø 70/78X16 Straight/R=2
A0.03.18 |
2 automatic positions kit for C1+C2 rounding unit |
N. 1 |
|
Device for the automatic tool positioning from control panel for a rapid working change-over according to the applied edge thickness (from thin edge to 2 mm and vice-versa) with management of the different thin edge thickness from control panel.
It includes:
- motors with 2 positions vertical and horizontal automatic positioning
- “ED SYSTEM” tools R=2
A0.01.50 |
8 positions manual revolver for tool |
N. 1 |
|
A0.03.07 |
"SP/F" oscillating brushing unit instead of standard "SPE" |
N. 1 |
|
for the cleaning and polishing of plastic edges:
- two overlapped motors with manual tilting complete with two cloth brushes
- top motor connected to the pressure beam for the automatic adjustment according to the panel thickness
- manual exclusion
- pneumatic oscillation
A0.00.07 |
"AAR" anti-adhesive device |
N. 1 |
|
positioned before the panel edge trimming unit. It prevents the glue sticking to the upper and lower panel surfaces, though improving the cleaning. This unit is complete with two spraying guns and tank for the anti-adhesive liquid.
A0.00.14 |
"U" Spindle moulder unit |
N. 1 |
|
It carries out through or timed grooves on the upper, lower and front panel side
It is complete with:
- selection of the right/left tool rotation
- front and vertical copying device
- timed intervention during machining
- on/off pneumatic exclusion of the unit
- mechanical digital readout to facilitate the unit set up
- exhaust hood
- tool not supplied
Technical data of the unit:
Motor power 4 kW
Speed of cutters 12.000 rpm
Unit tilting 0-90°
Timed intervention precision to 20 m/min +/-2
Max removal 90 mm²
Max. tool diameter 125 mm
A0.00.13 |
"RCA/2C" glue scraping unit |
N. 1 |
|
It eliminates any excess of glue in the joìnt between panel and edge.
The unit foresees:
- two vertical rotating copiers
- self-adjusting throwaway knives
- air blowers for the knives cleaning
- independent pneumatic intervention (lower/upper)
- exhaust hood
Technical Data:
Min. panel thickness: 13 mm
Max working speed: 25 m/min
Vertical disk-shape feelers
Tool radius: 2 mm
A0.01.74 |
"PH/1600" double edge brightening unit |
N. 1 |
|
With the heating of PVC/ABS edges it allows the brightening of the colour.
The unit receives air from the compressed air distribution system and gives out hot air through two independent nozzles
Technical data:
Power W 1600+1600
Tension V 220
A0.00.93 |
Mobile infeed device for drawers |
N. 1 |
|
Manual device to facilitate infeeding of small squared panels (eg. shelves and drawers) up to the pressure beam grip.
Manual infeed movement by handle
Manual return movement by handle
After the use, it is easily tiltable on the side without parts removing
Technical data:
12 mm minimum panel thickness
220 mm minimum panel width
135-400 mm panel length
A0.02.23 |
Machining of panels with length or width lower than the standard ones |
N. 1 |
|
It allows the machining of narrow work pieces (non-edged side) with smaller dimensions than the standard ones.
Technical data:
Lengthwise machining
Minimum panel length (edged side) mm 400
Maximum panel thickness mm 22
Minimum panel width with panel projection mm 35
- with thin non rounded edge mm 60
- non rounded edge thickness up to 3 mm mm 75
Crossway machining
Minimum panel length (edged side) mm 125
Minimum panel width mm 220
A0.02.84 |
Kit for solid wood machining up to 22 mm |
N. 1 |
|
It includes:
- no. 2 additional pressure rollers driven by a pneumatically controlled cylinder
- 1,8 kW motors in place of the 1 kW standard ones for the in-line trimming unit
- Automatic exclusion of the copying device for “YU” solid wood
- Automatic exclusion for “RSU” solid wood
- Automatic exclusion for “RCS”
A0.00.99 |
Outfeed transfer |
N. 1 |
|
Optimizing device for the extraction of small work pieces installed at machine outfeed and made of:
- track with rubber pads
- additional pressure system fixed to the pressure beam
A0.02.59 |
Tools kit R=1,5 instead of R=2 |
N. 1 |
|
It replaces all R=2 mm tools with R=1,5 mm tools
A0.02.13 |
"ED-System" h=64 diamond tools instead of h=49 ones for "RT-E" pre-milling unit |
N. 1 |
|
Instead of the standard ones
D 100 H=64 Z 3+3
60 mm max. panel height
52.26.41 |
Operating cost for additional packing |
N. 1 |
|
A0.03.26 |
Pallet for base 78 |
N. 1 |
|
A0.04.42 |
Additional packing for autotransformer |
N. 1 |
|
|
Total price |
USD |
252.000,00 |
|
Above specs taken from literature, internet and inspection; and thought to be accurate but not guaranteed. As always please take advantage of the inspection period to verify.
The listed specifications & information were taken from the manufacturer’s published information, internet research, or seller’s description.
The specifications & information are assumed to be correct; however, in no way, guaranteed. Bidders are encouraged to inspect the machine, call with questions, or contact the manufacturer for more information.
Please log in to view the bid history
LoginPick-ups are to be scheduled by appointment only. Please contact Sabrina Burns at 209-839-7707 or [email protected] to schedule an appointment. For freight quotes please contact Aaron at All-Ways Trucking at 541-608-6532. Buyer bears all costs to remove and load this lot. Buyer must remove entire lot purchased. Anyone removing non-hand carriable lots must provide MachineryMax, Inc. with a certificate of insurance (COI) before purchased items can be removed.
For Rigging/Loading please contact:
Gorham Industrial, LLC - James Gorham - 803-617-8434 - [email protected] - www.gorhamindustrial.com
Preston Machinery, LLC - Tom Preston - 269-685-7591 - [email protected] - www.prestonmachineryllc.com
For Shipping Quotes, please contact: NCL Trucking, John, 615-452-7651
All buyers agree to make full payment to MachineryMax, Inc. within 48 hours of the online closing date for the auction lots purchased. All invoices over $1,500.00 are to be made by bank wire transfer or cashier’s check payable to MachineryMax, Inc. Purchases under $1,500.00 may be made using Visa MasterCard, or American Express (2% credit card processing fee will be added to the invoice). All payments are to be made in USD currency only. Bidder represents and warrants to MachineryMax, Inc. that such bidder has immediately available funds to fully pay for its successful bids within 48 hours of the online closing date. All payment questions should be directed to Sabrina Burns at 209-839-7707 or [email protected] All buyers agree that there will be a 15% Buyers premium that will be added to the final invoice.