(2015) Stefani "Solution HD" Edgebander - Pre-mill & Corner Rounding
Ended
Windsor Fixtures -Complete Plant Closure -Day 1- Lawrenceville, Ga
- Winning Bid : $22,000.00 USD Sold
- 46 Bid(s)
- High Bidder: c****s
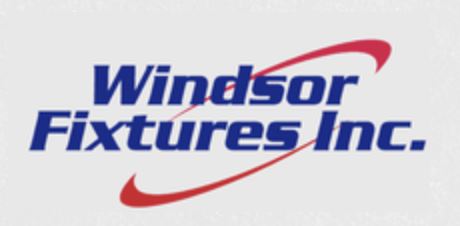
WINDSOR FIXTURES INC COMPLETE PLANT CLOSURE - LAWRENCEVILLE, GA - DAY 1 ( Closed #26329166 )
For Rigging/Loading please contact:
Gorham Industrial, LLC - James Gorham - 803-617-8434 - [email protected] - www.gorhamindustrial.com
Preston Machinery, LLC - Tom Preston - 269-685-7591 - [email protected] - www.prestonmachineryllc.com
For Shipping Quotes, please contact: NCL Trucking, John, 615-452-7651
-
Pick Up Location
755 Raco Dr, Lawrenceville, GA 30046
-
Make
Stefani
-
Model
Solution HD
-
Serial Number
AH/005896
-
Year
2015
-
Phase
3 PHASE
-
Voltage
208-230/460
-
Load Out Period
April 9, 2020
-
Estimated Dimensions
30'L x 5'W x 7'H
-
Estimated Weight
4,400 KG
-
Seller Comment
CONTACT ALWAYS TRUCKING for shipping quote 541-608-6532
-
Load Fee
A rigger is required for this lot. Gorham Industrial, LLC 803-617-8434 [email protected] or Preston Machinery, 269.685.7591, Tom Preston, [email protected]
-
page views
4579
In light of how many Edge Banders are in this auction, we want to be clear about what options each has. The specs below are a general guideline but verification of anything specific may be verified in person at the provided open houses. You may also choose to e-mail the Shop Engineer, Steve Hardy: [email protected]
This machine does NOT HAVE: PUR or Grooving saw
The dust extraction manifold as shown in the pictures is included. It includes the pipe that would encompass the machine and flex hoses. It does not include the remaining pipes to the dust collector.
The machine base is fabricated using a heavy duty, mono-block design. This provides a solid surface for mounting all of the working units. This structure, pressure beam and working support units are all poured at SCM’s own Foundry & controlled throughout the fabrication inside the SCM Group, ensuring the most stringent specifications.
All working units are attached using the Heavy Duty “H” style supports that ensure a vibration free work environment which reduces the amount of “adjustments” that need to be made on motorized units under the hood.
The top pressure beam is made of thick steel to eliminate “flex” when maximum pressure is applied.
Top pressure beam is fitted with a twin-profile V-belt for even pressure & precise holding of even small work pieces.
The feed track consists of 70 mm wide, self-lubricating nylon sliders. The replaceable track pads are coated with wear resistant vulcanized rubber to prevent work piece movement.
The track guiding system consists of one flat guide and one round guide. The flat portion is located closest to the machine working units for maximum pressure while holding the work piece perpendicular to the working units. The round guide is located on the opposite side of working units to ensure perfect linear alignment by eliminating the possibility of “twist”. Both guides are made of hardened ground steel and are equipped with an automatic lubrication system.
The cabinet is coated with noise-reducing material and is illuminated with non-glare fixtures. The cabinet is custom configured to allow appropriate dust extraction for each working unit.
PC CONTROL SYSTEM FOR THE FAST, EASY AND PRECISE HANDLING OF THE MAIN FUNCTIONS OF THE MACHINE.
IT INCLUDES:
Creating programs Just in Time. Possibility of management by means of
production list;
Virtual preview of the processed panel with automatic selection of operating units;
Flexible and independent management of each unit and tool without machine vacuum;
Clear and concise diagnostic information for a fast resolution of problems; Working statistical data: number of worked pieces and meters, of the employed hours etc.;
Management for automatic selection and instantaneous of the magazine edge coil;
Quick selection of the main functions of the main page with PRO EDGE function;
Unit of measurement in mm;
Operator "Win-Edge" interface in the following languages: Italian, French, English, Spanish, German (opt. Portuguese and Russian).
MAIN CHARACTERISTICS:
PC Office Operating system: W XP Screen: 17" TFT
2 network card ETHERNET
6 USB ports - 2 PS/2 ports
Bar code reader management
SCM Group North America
Phone: 770-813-8818
Website: www.scmgroupna.com
STEFANI HD-78
B25282 VARIABILE FEED SPEED 12-25 M/min
The machine features variable track speed from 12-25 Meters/min. (39 – 82 feet/min) Track speed is set in the programs to suit the application.
W50605 ELECTRONIC POSITIONING OF TOP PRESSURE BEAM
Automatic motorized positioning of the top pressure beam from the control. This system also automatically adjusts all work units to accommodate the new part thickness. Beam height is set in the programs to suit the application.
B09094 75 kVA AUTOTRANSFORMER
Multi-tap transformer to accommodate US voltages – 208-230-460
W01405 PANEL SPACING DEVICE
A95111 TWO POSITION INFEED FENCE Pneumatic two position of infeed guide.
A50164 ANTI-ADHESION UNIT AA
A95117 PRE-MILLING UNIT
This unit uses milling units rotating at 12,000 RPM to remove a pre- determined amount of material from the edge of the part.
It is equipped with:
- Two 4kw motors on THK guides for automatically advancing and retracting the counter rotating motors.
- Lateral side copy device to compensate for any improper machine feeding or warp in long boards. (Up to 1mm)
- Mechanical digital indicators
- Acoustically insulated sound enclosure
- Blowers for panel cleaning.
A71420 DIAMOND MILLING CUTTERS
Two 100mm x 64mm cutters, One cutter per head. Maximum panel thickness is 60mm.
A81553 PANEL HEATING LAMPS
This devise pre-heats the edge of the panel to improve adhesion.
Standard GLUING UNIT VC 600
High effiecency gluing sytem for standard glue types.
- Glue pot with Teflon coating for easy cleaning
- ‘No Tool’ Glue pot removal system
- Precise control of the amount of glue on the panel edge
- Electronic control of the glue temperature
- Movement of the glue spreading roller, of the first pressure roller, and of the feed roller by motors
- Automatic temperature kick-down to avoid glue scorching
- Heavy duty guillotine for automatic tape trimming
- Automatic loading of coiled material or strips
- Pressure section with one large, motorized roller and three idle rollers with opposing tilt. All rollers have “jump” capability.
- Addition of two idle rollers for a total of six (Code A81547)
- Additional Quick Disconnect Glue Pot
WORKING UNITS:
A81603 EDGE PRESENCE SAFEY DEVICE
A00136 PRESET FOR THE NORDSON PUR BLUE 4 WITH EB 60 NOZZLE
System Features double thermoregulation for controlling two different working temperatures for EVA and PUR glue. Pre-wired for pre-melting management, pre-drilled for future installation, includes mechanical support for the locking of the application unit.
A81539 QUICK MELT SYSTEM
System Features:
- Quick-melt system with pot for melting glue granules. This allows for a fast melt of the glue granules with controlled alimentation into on the spreading basin
- The pump heated by resistors and complete with thermos-regulators for the temperature control
- A smaller glue pot with electronic glue level monitoring replaces the standard glue pot to improve heating time. Machine comes equipped with an additional quick disconnect glue pot.
A72291 TWIN AUTOMATIC VERTICAL COIL MAGAZINES
Edge feeding system with 2 stations providing automatic infeed for coiled material- 2 coil-holder magazines vertically placed
- Automatic feed system with automatic changeover at the end of the roll
- Automatic ‘low material’ warning
- Programmable changeover within the Win Edge programming
A81511 ELECTRONIC PRESSURE ROLLER POSITIONING
Electronic setting of the pressure section by means of numerical controlled motor to set the position of the pressure rollers when changing edge thickness. This system is fully controlled by the PC program or manually adjusted on computer screen. Mounted on THK guides
- Addition of two idle rollers for a total of six (Code A81547)
Standard YU/SP-750 TOP MOUNTED END TRIMMING UNIT Automatic removal material beyond the end of the work piece
- Unit installed on the pressure beam
- Two motors with timed pneumatic movement
- Front, back feeler with automatic location
- Lateral feelers on linear ball recirculating guides with pneumatic intervention
- Motors with manual tilt up to 15°
- Automatic exclusion per application via the program
A50571 AUTOMATIC HORIZONTAL BLADE TILT
Standard R TRIMMING UNIT
For the rough trimming of thin and medium edges or for the finishing of solid wood edge:
- Top and bottom trimming motors with quick-release device
- Top motor connected to the pressure beam for automatic adjustment according to the panel thickness
- Large diameter, disc-shaped vertical copying device
- Numerical indicators for the horizontal and vertical shifting of the motors
- Automatic exclusion per application via the program
- Upgrade to 1.84 kW motors (option A81559)
Standard RSU FINE TRIMMING UNIT
Automatic top and bottom trimming for thin edges or rough trimming on PVC/ABS edges:
- Two motors tilting up to 30° with quick-release system
- Top motor connected to the pressure beam for the automatic adjustment according to the edge thickness
- Large diameter, disc-shaped vertical copying device
- Horizontal and vertical automatic cut-off up to 10 mm.
A50785 ELECTRONIC POSITIONING OF FEELERS FOR RSU
This device automatically positions the tools for rapid change-over of the working process according to the thickness of the edge applied, from thin edge to 3 mm and vice versa.
Unit equipped with:
- Motors with 2 positions vertical and horizontal automatic positioning - lateral disk feelers with horizontal electronic positioning system
- Tool bodies with disposable insert cutters. 70/78x16 Straight/R=1.5
A73732 CORNER ROUNDING UNIT C1+C2 2P
This heavy-duty unit is designed to round the front and rear corners of work pieces with thick PVC edging. The four independent motors on this unit are equipped with front and lateral copying devices. In/out positioning is controlled through the PC. The unit is designed to change between 1.5mm PVC to thin tape via the PC.
- Four motors with quick-release system with motor blocks supported by a parallelogram supports that keep tool in perfect position independently from the geometry of the profile
- Motors equipped with 2 position automatic positioning to quickly change from thin tape to 1.5mm PVC.
- Separate processing sequences for each corner to avoid causing
vibrations of the panel
- Four motors guarantee a tear out free finish when applying 3mm wood coil
- Copying system with bearing feelers and lateral feeler
- Automatic exclusion
- Pneumatic positioning of the cutter on 2 positions for processing 1.5mm or thin pvc.
A73741 FOUR CUTTER HEADS INSTALLED WITH 1.5MM RADIUS TOOLS
Standard EDGESCRAPING UNIT RAS/S
Top and bottom scraping for PVC/ABS material
- Quick release device for motor and tool which allows the fast and precise change over
- Vertical and horizontal shifting devices made of steel grounded bars with recirculating ball bearings
- Large diameter vertical and horizontal feelers
- Numerical indicators for the horizontal shifting
- Automatic exclusion
- 1.5mm radius tools included
U SPINDLE SHAPE STATION
The unit is equipped with a 5.35 hp motor. It is capable of through grooves and timed grooves on the upper, lower and face of the panel. Selection of right or left hand rotation, timed intervention, pneumatic exclusion of the work unit, digital readouts for the positioning and an exhaust hood are standard. 12,000 rpms, tilting from 0-90 degrees, max tool diameter is 125mm and max removal is 90mm2. Timed intervention at 20m/m is +/- 2mm.
A51211 GLUE SCRAPING RCA/2C
Removes possible excess of glue on the top and bottom side of the panel:
- Complete with two cutters
- Vertical copying device
- Two blowers cleaning the cutters
- Automatic start to assure the best processing of the starting and the ending side of the panel
- Automatic exclusion
A51706 DOUBLE EDGE BRIGHTENING UNIT PH/1600
This unit brightens colors on PVC/ABS edging with super-heated air.
The unit receives air from the compressed air distribution system and gives out hot air through two independent nozzles.
A81576 BUFFING UNIT SPN
For the cleaning and finishing of plastic edges:
It is composed of two overlapped motors that tilt vertically.
A81577 PNEUMATIC CUTOFF AND OSCILLATION
Standard TELESCOPING PANEL SUPPORT
- Designed to telescope in & out for easy cleaning around machine & fast panel width changeover. - Telescopes to 650mm
- Glides on rollers are made of high impact plastic
A3550 OUT-FEED BELT TRANSFER
TECHNICAL SPECIFICATIONS
Working Height
Edge Thickness
Max. track speed (depending on edge thickness)
Feed Motor Horsepower
Minimum Panel Length:
Minimum Panel Spacing
Min. coil length
Min. strips length (Solid wood and HPL)
Pre-Mill Unit
Motor Power
Rotation
End Trimming Station:
Motor Power
RPM
Automatic blade tilt
Edge Trimming Unit (1st):
Motor Power
RPM
Tilting
Edge Trimming Unit (2ndt):
Motor Power
Tilting
Cutting Tools, straight knife inserts (4)
Corner Rounding Unit:
Motor Power
RPM
Tooling Radius
Profile Scraping Unit:
Knife Radius
Spindle Moulder Unit:
Motor Power Motor RPM
Tilt
Max Removal
Max Tool Diameter
Glue Scraping Unit:
Knife Radius
Buffing Unit:
10-60 mm (3/8" – 2 3/8")
0.4-22 mm (7/8")
12-25 m/min (40-82 FPM)
4 kW
140mm (5 1/2”)
220mm ( 8 5/8”) with Corner rounding
630mm (24.5/8”)
230mm
250mm
4 kW
12,000 RPM
0.5 kW ea.
12,000 RPM
0-22 degrees
1.84 kW
12,000 RPM
Flush
0.5 kW
0-30 degrees
70mm x 12mm
1.5mm radius
.35 kW ea. (4 motors)
12,000 RPM
1.5mm
1.5mm
4 kW 12,000 0-90 90mm2 125mm
Straight
Motor Power |
0.29 kW |
RPM |
1,500 RPM |
Brush Dimensions |
150mm x 50mm x 33mm |
Pneumatic Operating Pressure |
90 PSI |
Machine Price new:$245,000.00
Above specs taken from literature, internet and inspection; and thought to be accurate but not guaranteed. As always please take advantage of the inspection period to verify.
The listed specifications & information were taken from the manufacturer’s published information, internet research, or seller’s description.
The specifications & information are assumed to be correct; however, in no way, guaranteed. Bidders are encouraged to inspect the machine, call with questions, or contact the manufacturer for more information.
Please log in to view the bid history
LoginPick-ups are to be scheduled by appointment only. Please contact Sabrina Burns at 209-839-7707 or [email protected] to schedule an appointment. For freight quotes please contact Aaron at All-Ways Trucking at 541-608-6532. Buyer bears all costs to remove and load this lot. Buyer must remove entire lot purchased. Anyone removing non-hand carriable lots must provide MachineryMax, Inc. with a certificate of insurance (COI) before purchased items can be removed.
For Rigging/Loading please contact:
Gorham Industrial, LLC - James Gorham - 803-617-8434 - [email protected] - www.gorhamindustrial.com
Preston Machinery, LLC - Tom Preston - 269-685-7591 - [email protected] - www.prestonmachineryllc.com
For Shipping Quotes, please contact: NCL Trucking, John, 615-452-7651
All buyers agree to make full payment to MachineryMax, Inc. within 48 hours of the online closing date for the auction lots purchased. All invoices over $1,500.00 are to be made by bank wire transfer or cashier’s check payable to MachineryMax, Inc. Purchases under $1,500.00 may be made using Visa MasterCard, or American Express (2% credit card processing fee will be added to the invoice). All payments are to be made in USD currency only. Bidder represents and warrants to MachineryMax, Inc. that such bidder has immediately available funds to fully pay for its successful bids within 48 hours of the online closing date. All payment questions should be directed to Sabrina Burns at 209-839-7707 or [email protected] All buyers agree that there will be a 15% Buyers premium that will be added to the final invoice.