(2016) Morbidelli "Uniflex HP" Feed-Thru CNC Machining Center
Ended
Windsor Fixtures -Complete Plant Closure -Day 1- Lawrenceville, Ga
- Winning Bid : $116,300.00 USD Sold
- 107 Bid(s)
- High Bidder: S****c
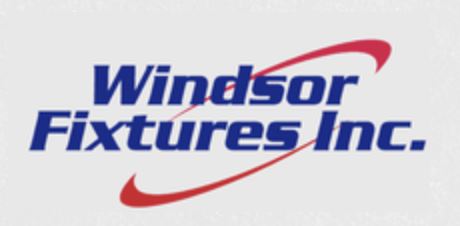
WINDSOR FIXTURES INC COMPLETE PLANT CLOSURE - LAWRENCEVILLE, GA - DAY 1 ( Closed #26329166 )
For Rigging/Loading please contact:
Gorham Industrial, LLC - James Gorham - 803-617-8434 - [email protected] - www.gorhamindustrial.com
Preston Machinery, LLC - Tom Preston - 269-685-7591 - [email protected] - www.prestonmachineryllc.com
For Shipping Quotes, please contact: NCL Trucking, John, 615-452-7651
-
Pick Up Location
755 Raco Dr, Lawrenceville, GA 30046
-
Make
Morbidelli
-
Model
Uniflex HP
-
Serial Number
AA2/003694
-
Year
2016
-
Phase
3 PHASE
-
Voltage
208-230/460
-
Load Out Period
April 9, 2020
-
Estimated Dimensions
29'x12'x120"
-
Estimated Weight
-
Seller Comment
CONTACT ALWAYS TRUCKING for shipping quote 541-608-6532
-
Load Fee
For Rigging/Loading please contact: Gorham Industrial, LLC - James Gorham - 803-617-8434 - [email protected] - www.gorhamindustrial.com Preston Machinery, LLC - Tom Preston - 269-685-7591 - [email protected] - www.prestonmachineryllc.com
-
page views
6262
CNC thru feed machining center with the ability of drilling, grooving and routing of panels from top and bottom, allowing to produce two parts at the same time.
Structure
The structure consists of an engineered frame strongly ribbed and very rigid; the closed ring structure has a large base to achieve and maintain, year after year, stability and precision under all work conditions.The newly designed frame enables automatic input of the panel and it has been designed to obtain the lowest overall dimension.
Movement
The panels movement along the longitudinal machine axis (X) is realized by a couple of clamps independent from each other. The patented design allows the working inside of the clamp optimizing the production cycle.These clamps, managed by the numerical control, acting as rear reference stop for the panels alignment. The movement of the operating units along X and Z axes is driven by brushless motors and recirculating ball screws, independent between upper and lower units; It is possible in this way to process simultaneously 2 panels with same dimensions but specular or with different working.
Office PC
-
Windows 7 operating system
-
17" LCD color display
-
Xylog Plus 2 interface machine software
General features of the Xylog Plus 2 software
Programming
-
parametric, graphic and ISO programming
-
import of the DXF and ASCII files (2D)
-
guided editor with graphic and syntactic help screens
-
automatic optimization of boring cycles
-
panel origin change to carry out processing of workpieces with special shapes or profiles
Included accessories
-
use of bar codes with already integrated software
-
self-diagnosis and signaling of possible errors or damages in the user's language
-
single step operation for manual control of individual program steps
-
on-line calculator of computed data
-
simulated program execution
Configuration
-
operator interface in user's language (I - GB - F - D – E)
-
machining head graphic configuration
-
double override which allows to adjust the operating unit positioning speed
Cordless reader device by which scans labels associated to the panel to load automatically a program on the PC with consequent reduction of loss of time.
Safety Devices
The UNIFLEX machine is protected on the all sides by effective CE safety systems (protection nets + sensible mats+ photoelectric cell + sensors) that prevent any contact between the operator and the machine moving parts during normal operation
Uniflex Clamping System
The movement of the panel along the X axis is accomplished by a set of independent clamps (patent pending Morbidelli). The clamps also act as rear reference stop to align the panels and are equipped with an automatic thickness measuring device.
Boring Heads
The operating unit is composed by two boring units totally independent between them; one upper and the other one lower, at independent spindles each equipped with:
-
12 vertical spindles along X
-
16 vertical spindles along Y
-
3 vertical hinge unit position 6
-
3 vertical spindles in Y
-
2 + 2 horizontal spindles in X
-
1 horizontal spindles in Y
-
1 horizontal spindles in Y
Y Prime
-
11 vertical spindles along X
-
3 vertical spindles in Y
-
2 + 2 horizontal spindles in X
Drilling head with patented RO.AX. Technology (RO.AX.)
-
Increased shaft diameter - Ø 20mm
-
No backlash on sliding guides
-
No vibrations
-
Exclusive “dust-protection” system
Advantages:
-
Better precision
-
Increased finishing
-
Faster drilling operations
-
Higher productivity
-
Increased effectiveness
-
1000 hrs re-lubrication period
52.08.71 Table with cross belts manual pre-loading station 610+610
This station allows the pre-loading of 2 overlapped panels with a width up to 610 mm, while the machine is working. As the panel in working phase crosses the loading area, some side pushers pick the panels up from the pre-loading area. During the automatic positioning, the panels are measured; these dimensions are transferred to the control which adjusts the programmed working scheme to the real workpiece dimensions. This allows to load of the working program in masked time. The station is equipped with front safety photocellUnloading station with cross belts.
The unloading table is made by supports spaced by cross belts.
-
The supports act as support to the panel during the whole working phases
-
The cross belts move the finished panels on the side of the machine allowing to the operator an easy and safety removal operation.
With this station it can be positioned a panel with a width up to 1300 mm allowing the machine to start the working of the next panel. It is possible also to manage 2 overlapped panels.
52.37.07 Electric cabinet with Air Conditioning Device
It maintains temperature of approx. 65°F inside the electric cabinet. Automatic Lubrication system
The lubrication of the X, Y, and Z axis is managed at fixed intervals by the Numerical Control, without any manual interventions and any stop of the machine to increase the machine reliability and to reduce at the minimum any maintenance time. 52.36.90 Partialized Dust Extraction
The dust extraction air flow is directed to the specific operating unit which is working at each time through dedicated valves.
63.03.43 Autotransformer 35kVA 208-230-460 V
Drilling Head Configuration (Upper Unit)
F58L Upper Drilling Unit (48+8X+2Y+Blade)
1T.UN.FX Option for position 1T - (52.39.12) Saw blade unit with automatic rotation 0/90°
Positioned on the head in pos.1, with independent drive and automatic positioning that allows to execute cuts in X and Y direction.
-
Maximum Saw blade diameter: 160 mm (6.29”)
-
Maximum Thickness 6 mm (.23”)
2T.UN.FX Position 2T - (59.29.26) Additional horizontal boring spindles in Y (1+1)
It includes:
-
2 Horizontal single drilling heads, clamp side, in position 2
-
Center to Center distance 32 mm, with 75mm selection
-
6000 rpm bits rotation speed by inverter
-
Bits attachment Ø 10
-
72 mm max tools length
-
Z max. 35 mm from pieces surface
3T.UN.FX Option for position 3T - (52.39.09) Electrospindle (10 HP) HSK 63F
This electrospindle is fixed on the head in pos.3, with independent drive.
Features:
-
Max power (S6) 7.5 kW (10 HP)
-
HSK F 63 quick release tool-holder
-
1500 - 24000 rpm spindle speed
-
(S1/S6) 6,6/7,5 kW (9/10 Hp) constant motor power from 12000 to 18000 rpm
-
Right and left rotation
-
Static inverter for continuous speed and rapid shutdown of rotation
-
Exhaust hood around whole perimeter
-
Cooling by airflow
-
150 mm max. tool length (including toolholder)
-
20 mm max. tool diameter
-
No. 2 HDK63F tool holders, ER32 connection complete with nut
-
No. 2 expansible collets, 15-16mm diameter, ER32 connection
4T.UN.FX Option for position 4T - (52.39.10) Additional horizontal spindles in X (2+2)
Additional Horizontal drilling blocks in the X direction on the fixed side5T.UN.FX Option for position 5T - (52.39.10) Additional horizontal spindles in X (2+2)
Additional Horizontal drilling blocks in the X direction on the adjustable unit
6T.UN.FX Option for position 6T - (52.38.33) Drilling Unit for hinges 45/9,5
It is positioned on the head in position 6, in place of the 3 vertical spindles. It allows the execution of 3 holes to introduce hinges in a single step. 57,5 mm max. tool length.
Drilling Head Configuration (Lower Unit)
F58L Bottom Drilling Unit (48+8X+2Y+Blade
1B.UN.FX Option for Position 1B - (52.39.12) Saw Blade Unit with Automatic Rotation 0/90°
Positioned on the head in pos.1, with independent drive and automatic positioning that allows to execute cuts in X and Y direction.
-
Maximum Saw blade diameter: 160 mm (6.29”)
-
Maximum Thickness 6 mm (.23”)
3B.UN.FX Option for position 3B - (52.39.09) Electrospindle (10 HP) HSK 63F
This electrospindle is fixed on the head in pos.3, with independent drive.
Features:
-
Max power (S6) 7.5 kW (10 HP)
-
HSK F 63 quick release tool-holder
-
1500 - 24000 rpm spindle speed
-
(S1/S6) 6,6/7,5 kW (9/10 Hp) constant motor power from 12000 to 18000 rpm
-
Right and left rotation
-
Static inverter for continuous speed and rapid shutdown of rotation
-
Exhaust hood around whole perimeter
-
Cooling by airflow
-
150 mm max. tool length (including toolholder)
-
20 mm max. tool diameter
-
No. 2 HDK63F tool holders, ER32 connection complete with nut
-
No. 2 expansible collets, 15-16mm diameter, ER32 connection
4B.UN.FX Option for position 4B - (52.39.10) Additional horizontal spindles in X (2+2)
Additional Horizontal drilling blocks in the X direction on the fixed side
5B.UN.FX Option for position 5B - (52.39.10) Additional horizontal spindles in X (2+2)
Additional Horizontal drilling blocks in the X direction on the adjustable unit
6B.UN.FX Option for position 6B - (52.38.33) Drilling Unit for hinges 45/9,5
It is positioned on the head in position 6, in place of the 3 vertical spindles. It allows the
Execution of 3 holes to introduce hinges in a single step. 57,5 mm max. tool length.
Technical Features
Min / Max length |
250mm-3000mm (9.8”-118”) |
Min / Max length panel without panel recovering |
250mm-1950mm (9.8”-76.77”) |
Min / Max width panel |
120mm-1300mm (4.7”-51.1”) |
Min / Max single panel thickness |
10mm-80mm (0.39”-3.14”) |
Min / Max overlapping panels thickness |
5mm(x2)-35mm(x2) (0.19”-1.37”) |
Max weight panel |
100kg (220 pounds) |
Working table height |
950mm (37.4”) |
Z stroke – upper boring head |
145mm (5.7”) |
Z stroke – lower boring head |
90 (3.5”) |
Clamps Programming speed (X direction) |
120 m/min (393 FPM) |
Heads programming speed in Y direction |
35 m/min (114 FPM) |
Heads programming speed in Z direction |
30 m/min (98 FPM) |
Compressed air intake |
6.5 bar (95 psi) |
Medium compressed air consumption |
500 NL/min (17.6 CFM) |
Max instant compressed air consumption |
800 NL/min (28.2 CFM) |
Dust extraction hood diameter - upper heads |
300mm (11.8”) |
Suction air consumption – upper head |
5100 CMH (3000 CFM) |
Dust extraction hood diameter - lower heads |
200mm (7.87”) |
Suction air consumption – lower head |
3400 CMH (2000 CFM) |
Suction air speed |
20 m/s |
***Specifications as per manufacturer website, please do own due diligence as to exact specs. of this machine
The listed specifications & information were taken from the manufacturer’s published information, internet research, or seller’s description.
The specifications & information are assumed to be correct; however, in no way, guaranteed. Bidders are encouraged to inspect the machine, call with questions, or contact the manufacturer for more information.
Please log in to view the bid history
LoginPick-ups are to be scheduled by appointment only. Please contact Sabrina Burns at 209-839-7707 or [email protected] to schedule an appointment. For freight quotes please contact Aaron at All-Ways Trucking at 541-608-6532. Buyer bears all costs to remove and load this lot. Buyer must remove entire lot purchased. Anyone removing non-hand carriable lots must provide MachineryMax, Inc. with a certificate of insurance (COI) before purchased items can be removed.
For Rigging/Loading please contact:
Gorham Industrial, LLC - James Gorham - 803-617-8434 - [email protected] - www.gorhamindustrial.com
Preston Machinery, LLC - Tom Preston - 269-685-7591 - [email protected] - www.prestonmachineryllc.com
For Shipping Quotes, please contact: NCL Trucking, John, 615-452-7651
All buyers agree to make full payment to MachineryMax, Inc. within 48 hours of the online closing date for the auction lots purchased. All invoices over $1,500.00 are to be made by bank wire transfer or cashier’s check payable to MachineryMax, Inc. Purchases under $1,500.00 may be made using Visa MasterCard, or American Express (2% credit card processing fee will be added to the invoice). All payments are to be made in USD currency only. Bidder represents and warrants to MachineryMax, Inc. that such bidder has immediately available funds to fully pay for its successful bids within 48 hours of the online closing date. All payment questions should be directed to Sabrina Burns at 209-839-7707 or [email protected] All buyers agree that there will be a 15% Buyers premium that will be added to the final invoice.