2019 Homag Edgeteq S-300 Optimat "KDF 440C" Edgebander
Ended
Complete Plant Closure - Salt Lake City, UTAH
- Winning Bid : $48,001.00 USD Sold
- 80 Bid(s)
- High Bidder: b****d
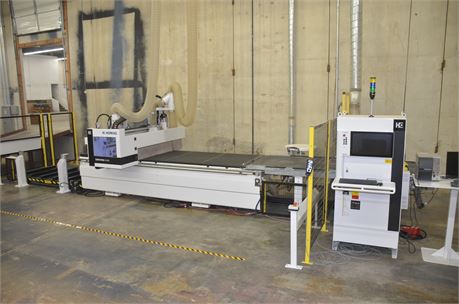
Complete Plant Closure - Late model Stiles Machinery - Salt Lake City UTAH ( Closed #22976631 )
Featuring 2019 Homag Centateq N-300 Optimat CNC Router Cell System - 2019 Homag Edgeteq S-300 Optimat "KDF 440C" Edgebander - Friz "Optimat "MFP 14/27" Membrane Press - 2019 Nederman "S1000" 10HP Dust Collector - 2019 Gardner Denver "D20" Air Compressor - Yale Forklift, Plus much More!
-
Pick Up Location
Salt Lake City Utah 84119
-
Make
Homag
-
Model
Edgeteq S-300 Optimat KDF 440C
-
Serial Number
0-261-71-4981
-
Year
2019
-
Phase
3 PHASE
-
Voltage
208-230/460
-
Load Out Period
8-14-20
-
Estimated Dimensions
19' x 4' x 7.5''
-
Estimated Weight
4078lbs
-
Seller Comment
Rigger Onsite Non Negotiable Load Fee - Contact Bivian at Capital Equipment 801-652-6547
-
Load Fee
$1000
-
page views
6788
Thickness Coils 0.4-3mm
Thickness Strips 0.4-8mm
Min Woklpiece Length 160mm
Min Workpiece Width 70mm
Workpiece Thickness 8-60mm
The EDGETEQ Series machines produce perfect edges for small shops to large-scale furniture and component industries who require the highest-quality results. With a wide variety of equipment designed to meet each customer's specific needs for materials, feed speed, aesthetics, and functionality, the EDGETEQ Series has a solution for every challenge.
Features & Details:
HOMAG EDGETEQ Series
Strength and stability
The EDGETEQ Series machines are built to withstand even the most challenging applications. HOMAG’s industry-leading transport chain design provides accuracy and stability as workpieces make their way through the machine along centrally-lubricated guides. Track pads securely hold the workpiece in place while a steel pressure beam applies even pressure and superior hold at optimum feed rates. For larger applications, the workpiece support and roller guides can be expanded for even greater stability.
Customizable features
The EDGETEQ Series machines transport workpieces effortlessly through a series of programmed processing stages located within the machine. Each stage performs its unique function with absolute accuracy and efficiency. Additionally, the EDGETEQ Series offers multiple features and capabilities within each stage of operation, giving manufacturers the flexibility to customize the machine to meet their specific needs today, while equipping themselves for future growth.
Cost-efficient operation
Set-up, operation and troubleshooting can be performed by a single operator. The EDGETEQ Series easy set-up results in less material waste and faster, safer machine adjustment.
Features & Details:
HOMAG EDGETEQ 4.4 Servo
Basic Construction: strong and stable
-
Integrated switch cabinet into the machine frame
-
Variable feed speed
-
Extendable solid work piece support track ;extends 600mm
-
Automatic chain track llubrication
-
Isolation transformer with variable infeed voltage for balancing all 3phases of incoming power and increasing the lifetime of the machine’s electrical components
-
Electrical equipment installed according toUL regulations
Sound Cover
The sound cover is equipped with two doors and a safety interlock system. When the sound enclosure door is opened, the corresponding unit shuts off. End trimming and fine trimming motors are equipped with electronic motor brakes to stop cutter rotation when the hood is opened or when the unit is shut off at the operator control panel.
Solid infeed fence
• Adjustmentofinfeedfenceviaservomotor
Track
• Industrialchainwithindustrialchainpads • Roundandflatguidance
• Automatic feed track lubrication systemTop Hold Down
• 2 rows of staggered *rollers (*belt for 4.4 FCG airTec)
• Smooth upper pressure *rollers (*belt for 4.4 FCG airTec)
• Toppressurehold-down;motorizedforworkpiecethicknessadjustmentMagazine
• Automaticmagazineforstripandcoilfeeding
• Line-controlledguillotine
• Largecoiltable(800mmdiameter)withbuilt-inrollerstoallow3mmPVCcoils • Edgestripcapacity:0.4–8mm
Features&Details: HOMAGEDGETEQ4.4Servo(continued)
powerTouch Controller: Simple operator control
This machine features powerTouch touchscreen operation, the most user-friendly and intuitive machine control available. Fit, finish and functionality of the powerTouch control unite to provide a user interface like no other. Ergonomic touch operation controls zooming, scrolling and swiping. It’s essentially a tablet computer configured to operate a machine. It’s that easy to use. The powerTouch control system is the standardized interface across all HOMAG machinery.
Hardware
• FullHDwidescreenmulti-touchdisplay,keyboard,mouseandanindustrialPC • PLCcontrolaccordingtointernationalstandardIEC61131
• USBconnectionattheoperatingpanel
• Ethernetconnection10/100MBITRJ45
Joint Trimming Unit
The joint trimmer provides a clean, even edge for optimal edgebanding application. Trimming removes material tears, marks from scoring saws and material swelling.
• Infeedfencepositioningviaservoprogramcontrol
• 2motors:1clockwisemotor,1counter-clockwisemotor
• Verticalspindleadjustmentviadigitalsettings
• Electronic frequency changer for all trimming motors, including electronic motor braking • Diamondinserttoolingaccommodatesworkpiecethicknessupto40mm(60optional)
• Heightadjustment:3mm
• 100x44x30mm;Z=3
Panel Pre-Heating
• Panel pre-heating zone prior to glue application •
5"zone length for optimum panel heating
QA-65 N Gluing Unit
The hot melt granulate glue application system is designed for PUR and or EVA adhesives and includes an automatic purge cycle. Pneumatic locking of the unit secures the workpiece at the last inch.
For safety, an automatic temperature reduction feature lowers the glue temperature by 50oC if no workpiece is run over a 15-minute span. The unit reheats in just three minutes.
• 2-levelsystem:350gwith8-minuteheatuptime;800gwith12-minuteheatuptime
• Hopperfeedingsystem(applicabletoonlytheQuickMeltconfiguration)
• LEDthermostatdisplayindicatesgluetemperatureofbothpre-meltingunitandglueroller • Direction of glue rollers is reversible
• Purgingofhotmeltgluewhileinthemachineforgluetype/colorchange
Pressure Zone
• Solid pressure zone with one driven main pressure roller and two idle post - pressure rollers •
Motorized positioning of the pressure zone
Double-Motor End Trimming Unit
This straight/chamfer end trimming unit is equipped with 2 motors and electronic motor brakes. For safety, the unit applies a drawing cut system for reduced blade projection when processing thick workpieces.
• Stronglinearguidancesystem,5timesmorerigidthanroundbars • Toolingincluded
• Program-controlledindexingfromstraighttobevelendtrimming
• Twopositionindexingforoverhang
• Dustextraction
MS 40 Multi-Stage Fine Trimming Unit with 2 Radii
This top and bottom trimming unit is equipped with 2 motors and electronic motor brakes.
• Equippedwithtwo(2)0.55kW(3/4HP)12,000rpmtrimmingmotors • Electronic motor brakes
• Auto-tiltfeature
• Servo-controlledtoedgethickness
• Nestedtopcopysystem
• Four(4)profilechoices:Profile1,Profile2,Bevel,andFlushTrimmingviaprogramcontrol • Equippedwith2multi-profileradiuscutterheads,including4knifecarbideinserts
Single-Motor Contour Trimming Unit with Servo Control
This unit provides corner rounding
• Includesone(1)trimmingmotor0.35kw(1/2HP)12,000rpm;electronicmotorbrakes • Servoaxiscontrolforprofiledepthandedgethickness
• Diamondtoolingincluded
• Programcontrolledfortwoedgethicknesses
Finish Scraping Unit
Flat knives remove any unwanted material from the trimmed / scraped edge.
Buffing Unit
This unit smooths edges and optimizes color.
• 2polishingmotorsfortopandbottombuffingoflongitudinaledges • 2clothbuffingdiscs:150x20mmdiameter
• Inclinableverticallyandhorizontally
Software Preparation for Spray Units
• MachineissoftwarepreparedfortheLubrication,Anti-Static,Separating,andDetergent Spray Units.
MZ 40 Multi-Stage Profile Scraping Unit with 2 Radii
• Programcontrolledindexingofinoroutofposition
• Multi-profilefor2radii
• Servo-controlledpositioningofbothverticalandhorizontaltracingrollers • Nestedtopcopysystem
• Multi-profileinsertsarestandardandincluded
0.4 - 8 mm (0.016 - 5/16") edge; 8 - 60 mm (5/16 - 2-3/8") panel thickness; 160 mm (6-3/8") min. panel length and 70 mm (2-3/4") min. panel width.
Feed Speed, variable 8 - 14 MPM. (26 - 46 FPM), 11 MPM (36 FPM) when using contour trimming.
Pre-Milling Station, (2) motors @ 2.25 kW (3.0 HP), 12.000 RPM, LH & RH rotation w/pneumatic jump control for chip-free and clean panel edges. Equipped with diamond cutter heads
Automatic Edge Magazine, for strip & coil stock, strips 0.4 mm - 8 mm (0.016 - 5/16"), coils up to 3 mm PVC and "HD" guillotine. "Quick Change" Glue Tank for maintenance & glue color change.
Pressure Section, 1st. roller driven plus (3) idle rollers, timed pneumatic pressure controlled; Servo motor positioning for programmable edge thickness changeover.
End Trimming: (2) Motor @ 0.35 kW (1/2 HP) 12,000 RPM, automatic chamfer from control panel 0°- 15°.
Flush/Bevel-Fine/Radius Trimming Unit: Top/bottom (2) motors, 0.55 kW (3/4 HP) 12,000 RPM, auto tilt postioning 0° - 25°, with combination flush/radius/chamfer cutterheads; horizontal and vertical tracing wheels, equipped with brushless multi-axis Servo motors.
Corner Rounding Unit: (1) Motor 0.35 kW (1/2 HP) 12,000 RPM for leading & trailing edges vertical corner rounding of panels; either radius or chamfer cutters can be mounted; 3 mm max. edge thickness.
Scraping, Multi-Profile (PVC): Top/bottom with (2) profiles. 1 mm and 2 mm or 3 mm instead of 2 mm, servo control positioning of vertical & horizontal copy wheels. PVC scrape collection box.
Scraping Glue Unit: Flush top/bottom on panel surface with floating insert knives.
Buffing Unit: Top/bottom (2) motors, 0.10 kW (0.125 HP) 2,800 RPM.
Motorized, programmable hold-down pressure beam; padded sound enclosure, used tooling and Original Factory machine documentation.
The listed specifications & information were taken from the manufacturer’s published information, internet research, or seller’s description.
The specifications & information are assumed to be correct; however, in no way, guaranteed. Bidders are encouraged to inspect the machine, call with questions, or contact the manufacturer for more information.
Please log in to view the bid history
LoginPick-ups are to be scheduled by appointment only. Please contact Sabrina Burns at 209-839-7707 or [email protected] to schedule an appointment. For freight quotes please contact Aaron at All-Ways Trucking at 541-608-6532. Buyer bears all costs to remove and load this lot. Buyer must remove entire lot purchased. Anyone removing non-hand carriable lots must provide MachineryMax, Inc. with a certificate of insurance (COI) before purchased items can be removed.
All buyers agree to make full payment to MachineryMax, Inc. within 48 hours of the online closing date for the auction lots purchased. All invoices over $1,500.00 are to be made by bank wire transfer or cashier’s check payable to MachineryMax, Inc. Purchases under $1,500.00 may be made using Visa, MasterCard, or American Express (2% credit card processing fee will be added to the invoice). All payments are to be made in USD currency only. Bidder represents and warrants to MachineryMax, Inc. that such bidder has immediately available funds to fully pay for its successful bids within 48 hours of the online closing date. All payment questions should be directed to Sabrina Burns at 209-839-7707 or [email protected] All buyers agree that there will be a 15% Buyers premium that will be added to the final invoice.