MORBIDELLI "UNIVERSAL 3615C PRESET" CNC MACHINING CENTER, YEAR 2017
Ended
2017 MORBIDELLI CNC AUCTION, DALLAS TX
- Winning Bid : $65,000.00 USD Sold
- 121 Bid(s)
- High Bidder: p****m
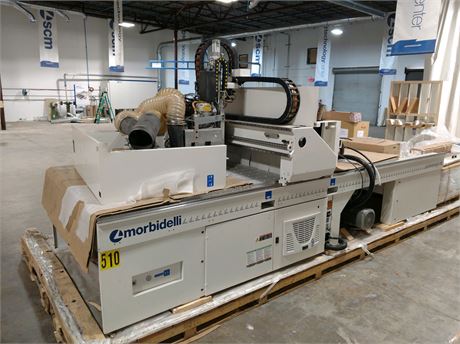
LATE MODEL MORBIDELLI UNIVERSAL 3615C PRESET CNC MACHINING CENTER, YEAR 2017 ( Closed #21306677 )
YEAR 2017 MORBIDELLI UNIVERSAL 3615C PRESET CNC MACHINING CENTER UP FOR AUCTION TO THE HIGHEST BIDDER. THIS IS A 2017 YEAR BUILT MACHINE THAT WAS USED AS A LOANER MACHINE TO A CUSTOMER FOR APPROXIMATELY 6 MONTHS. MACHINE IS NOW STORED IN DALLAS TEXAS WAREHOUSE. THIS AUCTION CLOSES ONLINE ONLY AT MACHINERYMAX.COM STARTING @ 10:00 AM PACIFIC TIME ON WEDNESDAY, APRIL 15TH, 2020. IF YOU HAVE QUESTIONS OR WOULD LIKE TO GO VIEW MACHINE IN WAREHOUSE PRIOR TO AUCTION CLOSE, PLEASE CONTACT KIRK @ 925-250-8248 OR [email protected]
-
Pick Up Location
4656 Leston St #518, Dallas, TX 75247
-
Make
MORBIDELLI
-
Model
UNIVERSAL 3615C PRESET
-
Serial Number
SEE PLATE
-
Year
2017
-
Phase
3 PHASE
-
Voltage
208-230/460
-
Load Out Period
APRIL 30TH, 2020
-
Estimated Dimensions
-
Estimated Weight
SEE PLATE
-
Seller Comment
-
Load Fee
$1200 LOADING FEE ADDED TO WINNING BIDDERS INVOICE
-
page views
5551
***PER THE SELLING PARTY, THIS MACHINE INCLUDES A MANUFACTURER 90-DAY "PARTS ONLY" WARRANTY. THE WINNING BIDDER WOULD ALSO HAVE AN OPTION OF BUYING A 12-MONTH EXTENDED WARRANTY FOR APPROXIMATELY $4000.00. THIS WOULD BE OPTIONAL BUT THE 90-DAY PARTS ONLY WARRANTY IS INCLUDED WITH MACHINE.
*MACHINE SOLD NEW FOR AROUND $134,000.00.
MORBIDELLI UNIVERSAL 3615C PRESET 5' X 12' CNC MACHINING CENTER
**THIS MACHINE WAS ORIGINALLY USED AS A LOANER MACHINE FOR APPROXIMATELY 6 MONTHS PRIOR TO BEING MOVED TO WAREHOUSE LOCATION IN DALLAS TEXAS.
208/230/460 VOLT, 3-PHASE MULTI-VOLT TRANSFORMER
16.5HP ELECTRO SPINDLE
REAR MOUNTED TOOL CHANGER HSK63F WITH 20 POSITIONS
F26L SPINDLE DRILLING UNIT
(2) BECKER VACUUM PUMPS
***ADDITIONAL SPECS. AS PER MORBIDELLI QUOTE TEMPLATE, PLEASE DO OWN DUE DILIGENCE AS TO EXACT SPECS. ON THIS MACHINE:
Morbidelli Universal 3615 C Preset – CNC Router
(52.33.57) Base Design and Construction
The Morbidelli Universal 3615 owes its rigidity to the design and weight of its reinforced base and innovative one-piece frame. All portions of the base are of heavy gauge steel and are normalized after welding, a process which ensures that all stress in the base is removed before it is machined and drilled for the guides.
Today's machining centers are being asked to perform a wide variety of operations (sawing, routing, and drilling) in both the vertical and horizontal planes at the highest speeds possible while, at the same time, maintaining a high quality of cut. Micro-vibrations are created around all types of CNC machining centers where there is head positioning, drilling, and high speed routing taking place on the machine base. Morbidelli solves the problem of deadening vibration as well as offering rigidity by employing heavy gauge steel members for the base of the machine. This weight, coupled with the one-piece frame offers the best combination of rigidity and balanced strength on a bridge design. . Movement along the X is high precision rack and pinion while the Y & Z-axes is driven by a ball screw.
High Precision, High Load Prismatic Bearing Guides
Morbidelli uses prismatic guides for support in all axes. Due to their added weight load capability (approximately 4 times that of conventional round guides), prismatic type guides can permit accurate head positioning at high speeds.
A.C. Servo motors in all three axes
A.C. servomotors, or A.C. brushless motors as they are sometimes called, are the latest in electronic linear motion technology. A.C. servomotors use less power and produce a more even output (drive) throughout the power band. The ability to maintain a constant torque setting when going from an idle setting into a heavy rout produces cleaner cuts and longer tool life. These motors are controlled by digital supply cards that offer the reliability and precision fine tuning associated with solid state electronics.
Solid State Inverter Controls Router Rpm
Solid State frequency inverters support the programmable router spindle speeds (S functions). By utilizing digital inverter technology, the programmer can select the correct cutter RPM and match it to the correct linear/rotational feed speed for the specific application and/or material being cut. This will give optimum quality of cut while greatly extending tool life. The inverter also acts as an electronic brake, stopping the router spindle motor in microseconds if an emergency signal is given.
Remote Diagnostics
Through the use of remote, real-time diagnostics can be provided from SCM’s facility in Duluth, Ga. The PC control is service over the internet. The customer is responsible for providing internet to the machine
Software:
General features of the Machine Panel and Xilog Plus Programming software
XILOG PLUS is the SCM workstation management software developed as a highly flexible, powerful and user-friendly programming system.
The beginner will immediately find himself at ease in front of the intuitive XILOG PLUS interface. There are many graphic aids that eliminate the need to learn particular instructions or programming language.
The more experienced computer user will also find himself at ease in a Windows® based operating environment, including all the features that this implies (i.e., cut and paste, multiple opening of files, etc.).
Those already familiar with previous SCM programs will be able to choose whether to manage the machine in the new graphic environment or to continue with the traditional input of programming instructions with the alphanumeric keyboard. Moving quickly from one environment to the other is very simple.
Graphic programming interface Machine operation interface
XILOG PLUS has two applications – to aid in programming and to allow operation of the machine.
Graphic programming interface
This application is a powerful graphic/text editor that aids in programming. It manages program file as well as tooling information. Especially helpful are the built-in macros, shortcuts that are used in performing repetitive tasks (routing arcs, drilling shelf holes, etc.). Users can also customize macros for their own particular needs.
Machine Operation Interface
This application allows the operator to recall programs and run them on the machine. It tells the operator basic information about the program such as the working field, part size, etc. It also has a very powerful machine diagnostic section with photos and troubleshooting aids.
Additional XILOG PLUS features:
Controlled acceleration and deceleration
Linear and circular interpolation
Self-diagnostics through error messages
Dynamic tool correction via PLC due to active wear concerning space and time.
Subroutine programming (canned cycle) with library
Specular programming: Allows writing of programs two different multiple reference points. For example the Left or Right corner of a panel.
Parametric scaling of programs through use of template type programs that the operator creates and stores in memory. Part programs can then be proportionally scaled up or down in size without the need to re-write the entire program.
Programs can be viewed from all 5 faces
Built in macros for simple, widely used programs
On board cycle optimization
Configuration
Machining Head graphic configuration;
double override which allows to adjust the operating unit positioning speed;
Machining Speed selection;
SCM CNC - JERK function management for dynamic control of acceleration/deceleration.
Office PC Based Controller
The Morbidelli Universal 3615 uses an office PC for the operator interface. This Windows 7 based platform utilizes a CN unit to communicate with the machine.
Control panel with lengthened cables
It allows the cables lengthening from 2,5 mt to 6 mt.
(63.03.73) Remote Control Pendent
This remote control pendent allows the operator to freely move around the machine and control the machines functions without being restricted to the computer console.
(63.01.27) Electric cabinet with Air Conditioning device It maintains temperature of approx. 65°F inside the electric cabinet.
16.5 HP (S6) Electrospindle Routing Unit
The routing unit is equipped with a power electro spindle and automatic tool changer.
The unit is mounted directly to the machine mobile upright.
It includes:
HSK F 63 quick release tool-holder
1500-24000 rpm spindle speed
(S1/S6) 8,5 /12 kW (11,5/16.5hp) constant motor power from 12000 to 18.000 rpm
Right and left rotation
Static inverter for continuous speed and rapid shutdown of rotation
Cooling by coaxial air flow
Exhaust hood around whole perimeter (200 mm diameter)
(52.24.48) Air tool blower
Keep the tool cooler, thus increasing the life of the cutter.
Helps to remove the sawdust from the cutting grooves in the nest.
Touch Probe
Allows to automatically measure and update tool Length
Panel Thickness Measurement Device
Measure and detect top of the material
(52.33.75) Rear Tool Changer HSK63 with 20 Positions
Features and Specifications:
Maximum number of tools that can be installed: 20
Tool attachment: HSK 63F
Max. Tool Diameter: 120mm (4.7”)
(52.35.30) F26L Spindle Drilling Unit
The vertical spindles are spaced on a 32 mm center-to-center distance. Each spindle can be independently programmed and actuated. The spindles are arranged as follows:
No. 18 independent vertical spindles (9 right and 9 left)
Attachment for bits: 10 mm diameter
Center-to-center distance between axes: 32 mm
No. 4 double horizontal boring heads (1+1), 2 in X and 2 in Y (attachment for bits:10 mm diameter )
Rotation speed: 4.500 rpm (8.000 rpm max. with inverter)
1 integrated blade in X (125 mm max. diameter)
5.500 rpm rotating blade speed (10.000 rpm max. with inverter)
2,2 kW motor power
Vertical pneumatic ON/OFF stroke of each spindle: 60 mm
Vertical pneumatic ON/OFF stroke of each horizontal spindle: 75 mm
Exhaust hood around whole perimeter (150 mm diameter)
RPM Adjustment of the Boring Head with Standard Inverter
It allows the rotating speed programming up to 8.000 rpm maximum for the drilling
bits and 10.000rpm for the blade, exploiting the same inverter of the electrospindle.
Aluminum Solid worktable for Component Nesting
The aluminum multi-function worktable has an answer to most component clamping and nesting scenarios. The table is designed of high tensile strength aircraft aluminum, and is slotted both transversely and longitudinally to accept many different fixturing devices.
In addition to nesting full sheets, the Universal 3615 can also be used for routing smaller components. For work on the face of the component, rubber gasketing material can be used to isolate the vacuum for part hold-down. This eliminates the need for special fixturing devices as is necessary on many machines. When machining the edges of parts, the patented MODULSET system raises the component so work can take place without damage to the worktable.
The magnetic system for opening and closing the vacuum passages allows for an extremely quick table set up when the vacuum is only required in a portion of the table. With a dedicated tool (supplied) it is a matter of seconds to perform the set up with no need for a screw driver. PATENTED
4 Left stops for "A" field of which no. 1 Side Stop and no. 3 Rear Stops
8 Vacuum Areas Controlled By Electronic Switches
The working table is divided in 8 vacuum sub-areas which can be activated (open) or
deactivated (closed) with pneumatic valves, to concentrate the vacuum in a specific
worktable area
(63.02.34) Working field "I”
No.1 side stop and no. 3 middle stops. N.B. The machine has a single working field.
Preset for Automatic Loading and Unloading Device
Central Optimized Dust Collection System
It provides a single dust collection point for the electrospindle and Drilling unit allowing in this way to use the Dust Collection system more efficiently. Inside the main dust collector there are pneumatic cylinders that control automatically the opening/closing of each exhaust outlet when the operating unit is switched on/off.
Dust Outlet – (1) 200mm
Two (2) 300 Cubic Meter/Hour Vacuum Pump
The vacuum hold-down system features a 300 cubic meter/hour vacuum pump. It offers the reliability of a substantial increase in vacuum power and allows the use of spoil boards for nesting full sheets.
(63.03.39) Prearranged for Second Vacuum Pump
Photocell barrier safety system
The Universal 3615 is equipped with photocells and a safety fence. This system includes barriers on three sides of the machine combined with photocells on the front side, which allows access to the work area.
The photocells stop the work cycle in the operational field of the machine; the barriers prevent physical access to the machine. This system is called active because it prevents any contact between the moving parts of the machine and the operator.
(63.03.43) Autotransformer
Autotransformer allows the choice of KVA 35, 208 / 230 or 460 volt, 3-phase, 60 cycle
Automatic Lubrication
Automatically controlled lubrication to guides, bearing blocks, and the Y and Z axes ball screws. Some locations require manual intervention.
Technical Specifications:
FULL SPEC. PAGE ATTACHED AS PDF FILE.
The listed specifications & information were taken from the manufacturer’s published information, internet research, or seller’s description.
The specifications & information are assumed to be correct; however, in no way, guaranteed. Bidders are encouraged to inspect the machine, call with questions, or contact the manufacturer for more information.
Please log in to view the bid history
Login**A $500.00 LOADING FEE WILL BE ADDED TO WINNING BIDDERS INVOICE. THIS IS FOR LOADING ONTO A FLAT BED TRUCK OR TRAILER ONLY, SIDE LOAD.
PAYMENT IS DUE WITHIN 48 HOURS OF AUCTION CLOSE TIME. WIRE TRANSFER OR ACH PAYMENTS ONLY.