Weeke OPTIMAT NBP084/VANTECH480 with auto unloading conveyor
Ended
Item located in Rexburg, ID
- Winning Bid : $40,150.00 USD Sold
- 101 Bid(s)
- High Bidder: j****s
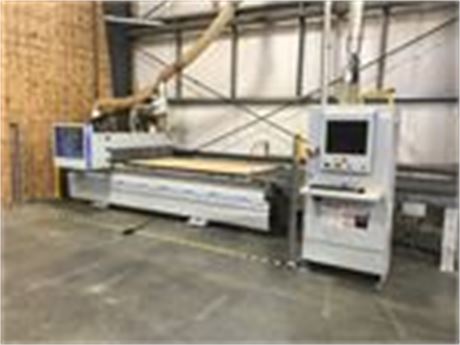
Weeke 2016 OPTIMAT/VANTECH480 Flat table LIKE NEW - Rexburg, ID ( Closed #20366948 )
Monkey Bars Storage in Rexburg, Idaho is pleased to offer this very late model, low hours, Weeke flat table CNC that is no longer needed for their continued production.
-
Pick Up Location
366 Dividend Drive Rexburg, ID 83440
-
Make
Weeke
-
Model
OPTIMAT NBP084/VANTECH480
-
Serial Number
0-250-80-3569
-
Year
2016
-
Phase
3 PHASE
-
Voltage
480 VOLT
-
Load Out Period
2-14-2020
-
Estimated Dimensions
-
Estimated Weight
-
Seller Comment
Seller has a forklift and will load for no charge.
-
page views
5551
Installed in 2017 with 312 hours actual use time. This late model flat table CNC includes 3 Becker vacuum pumps and an automatic unloading conveyor.
Below specs are as taken from manufacturer's site.
WORKING LENGTH 98.4"
WORKING WIDTH 49.1"
HSK 63 ROUTER SPINDLE POWER 13.4HP
ROUTER SPINDLE SPEED 1,250 - 24,000RPM
TOOL MAGAZINE CAPACITY 8
PNUEMATIC REFERENCE 11
3 BECKER VACUUM PUMPS
X/Y/Z VECTOR SPEED 96/96/25 M/MIN
Z STROKE 9.6"
DUST EXTRACTION CONECTION SIZE (1) 160 MM
AIR VELOCITY MINIMUM 97TF/SEC
STATIC PRESSURE MINIMUM 2200 PASCAL
DRILL UNIT-
-
Ball bearing arrangement provides for the compensation of forces from all sides and delivers the highest drilling quality. The more demanding the application, the more important this feature is.
-
The clever arrangement of the drill spindle ensures a constant distance between the drill bit and the bearing, whether the spindle is extended or not. Together with the diameter of the sleeve, this feature ensures the highest lateral stability and precision during the drilling process.
-
Integrated Mechanical Clamping System to ensure each drill spindle achieves proper depth regardless of material density and/or drill diameter
GUIDE SYSTEM
The X, Y, and Z axes are all supported
on THK-style linear motion guides. These guides are engineered to produce straight line tracking at high travel speeds while providing stability in both the radial and lateral directions.
-
The X axis is driven by two (2) helically- ground rack and pinion gear systems
-
The Y and Z axes are driven by high- precision ball screw
• Solid state drives and digital AC servo motors power the axes
• Digital drive technique in X, Y and Z direction features:
Maintenance-free motors with high-resolution optical encoders for precision and accuracy
Digital drive control units guarantee high reliability
MATRIX TABLE
A grooved phenolic MATRIX vacuum system is standard. It clamps down work pieces on the table surface. The grooves allow ef cient vacuum distribution; they also isolate table areas by inlaying a rubber seal and/or by accepting vacuum pods to af x small parts. Rubber gasket material is included.
• Working table length: 2500 mm (8' / 98.4 Inches)
-
Working table width: 1250 mm (4' / 49.2 Inches)
-
Workpiece thickness: maximum 100 mm (3.94 Inches)
-
Can be equipped with optional Pod System for elevating parts
-
-
Semi-Automatically divides the matrix table into 3 vacuum zones: 4’x8’, 4’x5.25’, 4’x2.5’
-
3 vacuum fields
-
VERTICAL ROUTER SPINDLE
The BENZ/ZIMMER GROUP HSK63 spindle motor is rated at 18 HP, but the machine operates it at a maximum capacity of 13.4 HP. This output meets virtually all application needs, reduces energy costs, and increases longevity.
-
Includes an automatic tool change feature with the tool change magazine
-
Direction of rotation: right hand / left hand
Speed: 1,500 - 24,000 rpm stepless programmable
Drive: frequency controlled to a maximum capacity at the tool: up to 8.5/10kW (11.4/13.4 HP) in continuous and intermittent operation (S1/S6 - 50%)
Spindle lubrication: permanent grease
Bearing: hybrid bearing (ceramic) with little friction, higher stiffness, and maximum operating life
Fan cooled
Central dust extraction
MULTI ZONE PROCESSING
The table and control interface on the Vantech Series allow the operator to simultaneously load multiple programs at up to 4 zero points (number of zero points determined during machine speci cation). The machine then optimizes drilling and routing routines and runs the multiple programs as a single le. This is an important feature for those who may use the Vantech Series machine as a “point to point” machining center or provide back-up to that style machine already in operation on their shop oor. An example of this in production is an operator loading smaller raw materials to the machines multiple reference points and running the parts in a single optimized machine cycle.
AIR JET
Four flexible air jets are integrated into the extraction hood, providing a cool, clean, and ef cient machining area. Air jets are activated via soft key at the control panel
AUTOMATIC TOOL CHANGER
To increase flexibility and decrease cycle time, an automatic tool changer (ATC)
is located near the left of the machine framework.
-
Tool holder: HSK63
-
7 tool places in tool magazine
-
Tool weight: maximum 5 kg (11.02 lbs.) including HSK cone
-
Tool diameter: 135 mm max when equipped with 7 tools
-
Tool change time: approximately 10 - 18 seconds
-
Tool loading: via integrated pick-up place at the tool
AUTO TOOL CHANGER LOADING POSITION
From a single position, operators can easily and quickly insert and remove tools.
Tools are manually inserted into the loading device, positioned close to the left front of the machine for easy access. The machine retrieves the tool and selects the rst available position in the tool magazine, deposits the tool, and updates the tool database.
To remove tools, the machine deposits tools in the loading position and automatically removes the tool from the active tool database. Sensors prevent the machine from depositing a tool when another tool is present.
TOOL LENGTH CONTROL
A heavy duty tool length control system is
a standard feature. To maintain accuracy, the machine measures the length of the tool and veri es it against the tool data stored in the machine control. This reduces human error, eliminates the need for multiple test
cuts, and saves set-up time.
7 SPINDLE VERTICAL DRILL BLOCK
Drill blocks increase the processing speed of the machine by allowing drilling operations to be accomplished without changing tools. Spindles in the drill block can be selected individually to meet different needs simultaneously.
-
Spindle clamping achieves precise drilling depth
-
Stroke Z-direction: 60 mm
-
Drilling depth: maximum 38 mm (up to 55 mm for special borers)
-
Direction of rotation: right hand/left hand
-
Speed: 3,450 rpm
-
Power: 1.5 kW
-
Shaft diameter: 10 mm
-
Total length of drill: 70 mm
-
Drilling diameter: maximum 35 mm
-
Distance between spindles: 32 mm
-
Type of spindle: individually selectable
-
Spindle con guration: 4X – 3Y
REFERENCE PINS
The machine has 11 reference pins for precise mounting. Pins are automatically actuated and surveyed by the machine control to prevent operation when the pins are not completely depressed.
-
2 are located at the rear of the machine
-
1 is located at the right rear right
-
6 are located at the front
-
1 is located at the front right
-
1 is located at the front left
The Vantech series features a Microsoft Windows 7 based state-of-the-art powerTouch control with software. The woodWOP 7 programming system (included) offers powerful drawing functions to simplify programming for operators without CNC experience and provide the premium features required to satisfy advanced users. A copy of the program is also included for installation on an of ce PC for off-line programming.
The woodWOP 7 generation of CNC programs enables:
-
Graphical tool selection from your database
-
Production list administration
-
Graphical presentation of work zones
-
Clear error messaging
-
3D NC-simulation and time calculation: 1 license
-
Automated spoil board maintenance program for quick and easy surfacing
The listed specifications & information were taken from the manufacturer’s published information, internet research, or seller’s description.
The specifications & information are assumed to be correct; however, in no way, guaranteed. Bidders are encouraged to inspect the machine, call with questions, or contact the manufacturer for more information.
Please log in to view the bid history
LoginPick-ups are to be scheduled by appointment only. Please contact Sabrina Burns at 209-839-7707 or [email protected] to schedule an appointment. For freight quotes please contact Aaron at All-Ways Trucking at 541-608-6532. Buyer bears all costs to remove and load this lot. Buyer must remove entire lot purchased. Anyone removing non-hand carriable lots must provide MachineryMax, Inc. with a certificate of insurance (COI) before purchased items can be removed.
All buyers agree to make full payment to MachineryMax, Inc. within 48 hours of the online closing date for the auction lots purchased. All invoices over $1,500.00 are to be made by bank wire transfer or cashier’s check payable to MachineryMax, Inc. Purchases under $1,500.00 may be made using Visa MasterCard, or American Express (2% credit card processing fee will be added to the invoice). All payments are to be made in USD currency only. Bidder represents and warrants to MachineryMax, Inc. that such bidder has immediately available funds to fully pay for its successful bids within 48 hours of the online closing date. All payment questions should be directed to Sabrina Burns at 209-839-7707 or [email protected] All buyers agree that there will be a 15% Buyers premium that will be added to the final invoice.