Biesse "Rover B 4.40 FT-k" CNC Router
Ended
Located in Carlsbad, Ca
- Winning Bid : $34,000.00 USD Sold
- 103 Bid(s)
- High Bidder: n****o
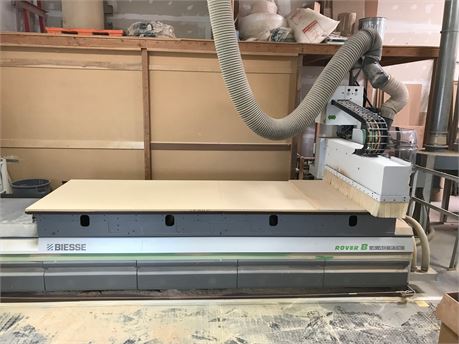
-
Item Location
Carlsbad, Ca
-
Make
Biesse
-
Model
Rover B 4.40 FT-K
-
Serial Number
57505
-
Year
2005
-
Phase
3 PHASE
-
Voltage
230/460
-
Inspection Date
By Appt Only call 209-988-4667
-
Final Removal Date
November 17, 2017
-
Estimated Dimensions
-
Estimated Weight
-
Seller Comment
This item requires a rigger for removal
-
page views
5990
BIESSE ROVER B 4.40 FT-K (SN# 57505)
(Flat Table)
9080080
The Biesse Rover B 4.40FTK represents the latest technological advancements in machining centers designed for the processing of engineered and solid woods, plastics, non ferrous metals, like aluminum and composite materials like Corian™.
Designed to play a critical role in today’s work cell and Just-In-Time manufacturing environments, the Rover B 4.40FTK is unsurpassed in productivity, safety, reliability and operational efficiency in its class. The Rover B 4.40FTK is manufactured by Biesse, a world leader in all types of equipment for the panel processing industry and, is supported locally in the United States by Biesse America, a totally owned subsidiary of Biesse.
Rigid Frame
The base structure of the Rover B 4.40FTK is manufactured of stress relieved, heavy gauge steel with structural steel cross-members precisely located to provide an extremely rigid platform.
Structural analysis by the most advanced CAD modeling systems has led to the development of a structure, which is able to withstand the most demanding work environments. Consequently, the Rover B 4.40FT performs at high speeds providing the highest output while maintaining a precision finish. The Rover B 4.40FT has a substantial fixed Y-axis beam to allow component-processing depths of up to 50.74” (1290 mm).
Guide Systems
Top quality, linear guides provide the high precision linear tracking systems for the X, Y and Z-axes on the Rover series machines. Linear guides systems are designed for extremely high load capacity and rigidity and ensure accuracy at high travel rates.
Drive Systems
The Rover B 4.40FT utilizes Yaskawa AC brushless servomotors with digital drive units. The powerful Yaskawa motors allow the Rover B 4.40FT to accelerate from a standstill to full speed in 350 milliseconds while the digital drive ensures a smooth acceleration and deceleration ramp.
The X-axis drive system utilizes a hardened, helical rack with hardened preloaded pinions for backlash compensation. The rack is bolted directly to the frame of the machine eliminating the transmission of vibration to the working units.
A hardened, precision re-circulating ball screw drives the Y and the Z-axis. The Z-axis stroke is 6.23” (160 mm) allowing the loading of panels up to 5.9” (150 mm) thick. In order to offset the weight of the head, a pneumatic counter-balance is utilized. This practically eliminates the gravitational forces of the head and ensures a long service life for the screw.
26462 Auto Lubrication System
Automatic centralized lubrication system.
At each time interval, programmable by NC, the lubricant is automatically sent to all linear guides and ball screws.
Working Field (S1)
For routing: X 3,685 mm (145”)
Y 1,380 mm (54.33”)
For drilling: Y 1,624 mm (63.9”)
NOTE: Full table coverage with all spindles
Parts Z-axis clearance: Z = 150 mm (5.9”)
Vacuum areas: 1
Work Table
Our oversized 49.5” x 145” (1258mm x 3685mm), single area, flat table is precision machined Bakelite (laminated plastic) which is designed for Nested-Based Manufacturing (NBM)
Our tables are designed to have NO restrictions. This allows you to fully utilize the capabilities of large volume vacuum pumps. The “high-flow” characteristics of our table allow you to do sheet production without having to use a gasket type spoil boards.
The Rover B 4.40 FT has 3 pop-up reference pins mounted in the back and 1 pop-up reference pin on the LH side of the machine
Vacuum Pumps
Two 300 m3/h at 60 Hz, rotary vanes, oil-free vacuum pump are included for a total maximum flow of 600 m3/h (350 cfm).
Available option to consider additional 300 m3/h pump for total 500 cfm (recommended over 3000 feet of altitude).
WORKING UNIT
12.2 HP (9 kW) Electrospindle, ISO 30 adaptor, air cooled
The innovative electrospindle is manufactured by HSD (High Speed Development), a Biesse Group company. The electrospindle incorporates an ISO-30 adapter allowing automatic tool changes or quick manual tool changes.
- The electrospindle is powered by an 11 kW inverter.
Benefits for the customer of the HSD technology:
- INCREASED PRODUCTIVITY with
- 7.5 kW (10.2 HP) from 12,000 to 15,000 rpm in S1 duty Continuous Duty.
- 9 kW (12.2 HP) / 12.000 rpm in S6 duty.
- Independent cooling fan that provides optimum cooling regardless of spindle rpm, ensuring maximum cooling in the most demanding start and stop applications.
- PRECISION AND QUALITY MACHINING
- The electrospindles on the Rover machining centers are attached directly at Z-axis carriage and extremely close to the Y-axis beam. This solution guarantees superior rigidity and is completely unaffected by the thermal expansions always present when the electrospindles are attached to the boring block effecting precision.
- Pneumatic stroke is on a prismatic linear guide for maximum strength and precision
- HIGH PERFORMANCES AND FLEXIBILITY with
- Programmable rotation speeds from 1,000 to 24,000 rpm
- RH and LH programmable rotation
- Efficient Dust collection through a programmable 5 positions dust hood
- REDUCED MAINTANANCE with
- Cartridge construction which allow for easy core replacement.
- Ceramic bearings, which are less susceptible to thermal elasticity than steel bearings, thus providing increased life and efficiency.
It includes a dust extraction hood with 5 different positions in Z controlled by the NC, in relation to the length of the tools or the different programs. The hood is automatically deactivated when the electrospindle is not working.
10 pos. Revolving Tool Changer
The electrospindle is served by a 10-position revolving tool changer installed on the Z-axis carriage plate. It can perform the tool change even during boring operations.
- Aggregate compatible
Boring Head
Biesse’s boring heads had always been the benchmark in terms of performance and durability.
Thanks to the innovative design Biesse Rover machines still feature the fastest boring cycle in the industry. The boring head is inverter driven for improved durability.
Newly designed boring head equipped with:
- 12 independent vertical spindles at 32 mm centerdistance, 6 of which are placed along X and 6 along Y, with oval cylinder for higher thrust.
- 4 horizontal spindles, 2 of which are placed along X and 2 along Y.
- 2,3 Hp motor; spindle rotation speed 4000 rpm
PC FRONT-END NUMERICAL CONTROL ‘CNI XP600’
The XP600 Numerical Control is a true residential PC, MS-Windows XP based technology.
Even the most complex programming functions are made simple by the use of pop up information request boxes. By simply entering information as requested, the operator can, quickly and efficiently, create intricate programs.
Thanks to the new Biesse technology WRT (Windows Real Time), which increases the performances of Windows XP by making it work in real time, the machine is controlled directly by the PC, and any other hardware component becomes unnecessary.
Since the software that controls the machine runs directly on a personal computer and not on a dedicated hardware device, the system architecture is greatly simplified, grants greater performance and reliability.
Main system specifications:
- WRT Software:
- Customized operating system Windows XP for the real time management of processes
- Module for the real time control of interpolated axes
- Module for input/output signals control
- Module for the real time execution of the machine logic
- Card for the Mechatrolink digital connection to the axes drives and for the connection to the input/output modules and to the other fieldbus devices
- Keys dedicated to the activation of the machine functions;
- user-friendly interface with pull-down windows NC1000
- programming of profiles and borings through assisted editor;
- macro calls for customized boring and routing patterns;
- boring optimizator, for selection of strokes, spindles, min. routes;
- parametric programming;
- graphical representation of 5 sides of panels to be worked;
- "trace" function;
- dynamic display of workings with tool centre route both for workings and simulations;
- graphic set-up of panel supports;
- reading of floppy disks with programs in RT-480 format;
- "normal", "mirror" and "translation" functions;
- active safety routines;
- on-line instruction manual;
- display of error messages.
PERSONAL COMPUTER
Main technical specifications:
- CPU Intel Celeron - 2.0 GHZ or superior; 256 MB RAM memory; 40 GB hard disk;
- 15" colour screen;
- Keyboard; Mouse; CD-ROM reader;
- Parallel port; Serial port RS-232; USB port; Ethernet card for network connection to an office PC.
* These technical specifications may be subject to updates.
Biesse has successful installations with the following software packages: AlphaCAM, AutoCAD, AutoCAD Lite, Cabinet Vision, Cabnetware , CadCode, CIMBlock, DesignCAD, MasterCAM, NC Micro, Pattern System Drill Mate.
Controls on Remote Keyboard
Remote keyboard for axes override along with a emergency push-button.
Basic Machine version
The graphic interface is fully compatible with the Windows standard and includes the following main modules:
- Assisted graphic Editor for the programming of boring, cutting and routing operations both on standard faces and on rotated or circular faces. It allows parametric programming and the import of files in DXF and CID formats
- Tool database with search filters helping tool selection
- Graphic tooling of operating heads and tool magazines
- Graphic set-up of panel supports
- Graphic configuration of machine data
BIESSEWORKS - basic - office version (1 hardware key)
Min. PC requirements:
-Pentium / Celeron processor
-128 Mb RAM with Windows NT / 2000; 256 Mb RAM with Windows XP
-150 Mb of free disk space
To use “solid” 3D simulation, we recommend a graphics card with processor that implements the OpenGl Stencil Buffer, preferably in hardware mode. We particularly recommend cards with an on-board graphics CPU from the GeForce family manufactured by NVIDIA.
Compatible with the numerical controls XP 600, NC1000, XNC rel. 1.2.0.2 and updated.3
BIESSE NEST
BiesseNest is the new user friendly nesting software that allows to nest parametric BiesseWorks programs as well as DXF files with proper layers.
The Rover B includes one licence for the office package.
7530111 USB Key for Biesse Works Qty. 1
Safety Devices
The safety system of the machine includes:
- Front safety mats equipped with control unit
- Side and back safety fence;
- Emergency rope placed in front of the machine;
- Sound-absorbing cover for the operating unit, with 3 rows of plastic strips
- Emergency button positioned on the nc
- Emergency button positioned on the remote keyboard
Air Conditioner
It allows the perfect working of all electronic components even at very high temperatures. Moreover, it protects the electric cabinet from dust, since no aeration fans are necessary and the cabinet is therefore airproof.
Auto-Transformer
For voltages different from 400 V/50 Hz
Documentation
- User's and maintenance manual
- Wiring diagrams
- Spare parts catalogue
- Manual for N.C. programming
Maintenance Equipment
Device for locking and unlocking tools from adaptors
- Set of wrenches
- Greasing pump
- 2 tins of grease for guides lubrication
Technical Data
- Electrical
- Max Installed electric power, machine only 30 KVA
- Compressed Air
- Pressure 7.5 bar (105 PSI)
- Air consumption 400 NL/Min (14 CFM)
- Dust collection
- Chip extraction socket diameter 250 mm
- Chip extraction air consumption: 5300 m3/h (3125 CFM)
- Air speed at the manifold 30 m/sec (99 foot/sec)
- Static Pressure 3000 Pa (12 inch water)
The listed specifications & information were taken from the manufacturer’s published information, internet research, or seller’s description.
The specifications & information are assumed to be correct; however, in no way, guaranteed. Bidders are encouraged to inspect the machine, call with questions, or contact the manufacturer for more information.
Please log in to view the bid history
LoginNo information available